Ammonia Refrigeration valves are the backbone of industrial refrigeration systems, ensuring safe, precise, and efficient control of ammonia flow. These are indispensable for industries like cold storage, food processing, pharmaceuticals, and chemical manufacturing, where ammonia’s superior thermodynamic properties are harnessed.
At Metro Refrigeration Industries, we engineer high-quality Ammonia Refrigeration valves designed to meet the demands of modern industrial applications. This blog covers ammonia refrigeration valve working principles, features, types, applications, and why Metro Refrigeration Industries is the trusted name for ammonia based refrigeration system solutions.

The Working Principle of Ammonia Refrigeration Valves
Ammonia refrigeration valves regulate the flow and pressure of ammonia within a refrigeration system. Here’s how they work:
Flow Control: Ammonia refrigeration valves operate by opening, closing, or partially restricting flow based on the system’s requirements.
Pressure Regulation: These are maintain optimal pressure to ensure smooth operation and prevent system overload.
Sealing Mechanism: Dual stem sealing and precision-engineered seats provide leak-free operation, even under extreme conditions.
Temperature Resistance: Designed to function across a wide temperature range, from -60°C to +150°C (-76°F to 302°F), these valves can withstand the thermal stresses typical of industrial processes.
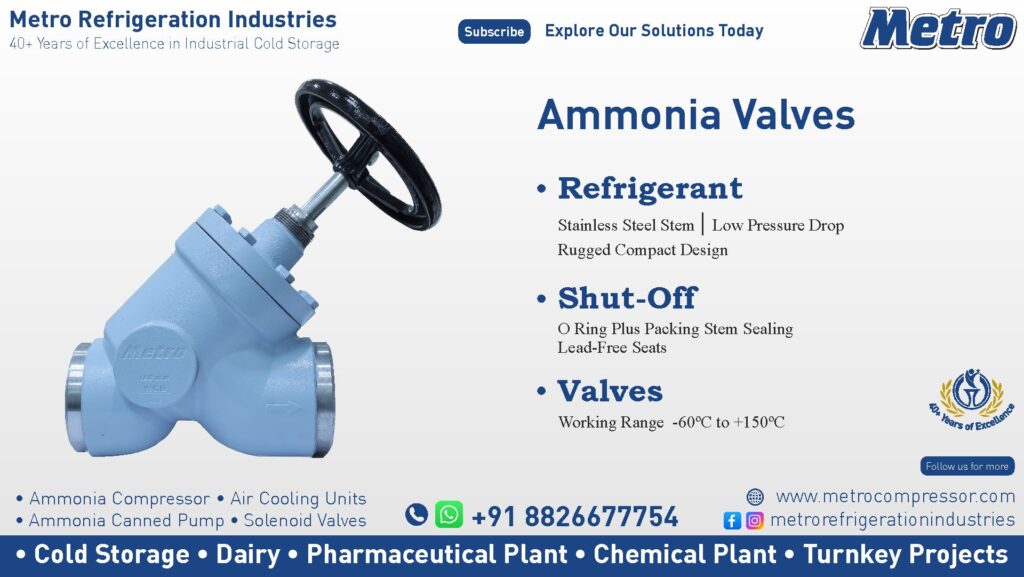
Ammonia Refrigeration Valve Principle
The fundamental principle of ammonia refrigeration valves is to balance pressure and flow dynamically, ensuring efficient cooling without compromising safety. With features like back-seating design and rising stems, these valves offer visual indicators and operational reliability.
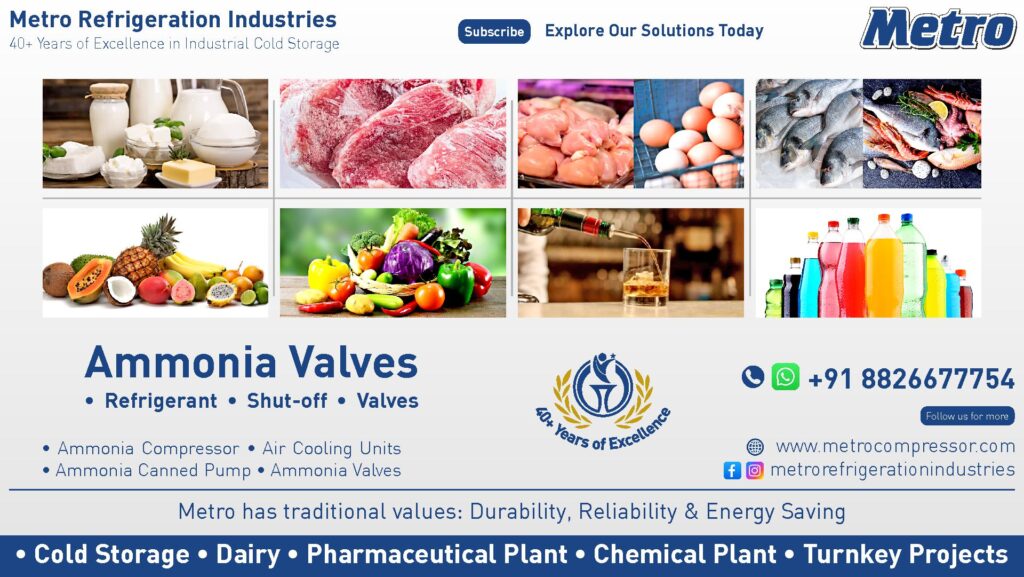
Why Ammonia Valves Matter
Ammonia refrigeration valves are essential for ammonia-based refrigeration systems, which are highly efficient, eco-friendly, and cost-effective. These valves not only enhance operational safety but also improve the longevity of the system by mitigating risks like pressure surges and leaks.
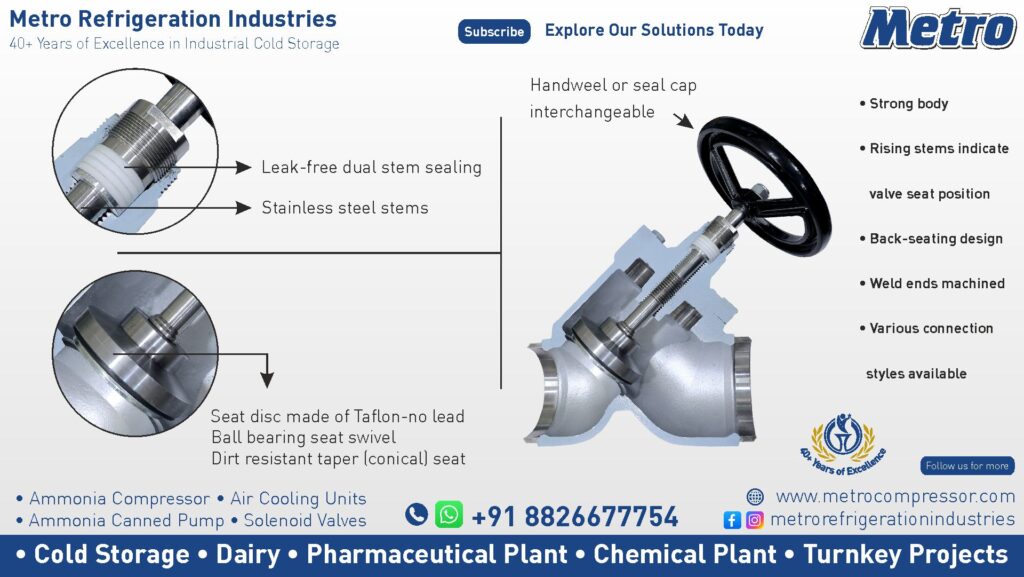
Advanced Features of Metro Refrigeration’s Ammonia Refrigeration Valves
Our ammonia valves are precision-engineered using state-of-the-art CNC manufacturing processes. Here are their standout features:
Strong Body: Made from durable steel casting for long-lasting performance.
Rising Stems Indicate Valve Seat Position: Offers clear visual feedback for operational accuracy.
Back-Seating Design: Extends valve life and ensures effective sealing.
Weld Ends Machined: Provides leak-proof and reliable connections.
Various Connection Styles Available: Flexible options to suit different industrial setups.
Leak-Free Dual Stem Sealing: Prevents ammonia leakage and enhances safety.
Stainless Steel Stems: Polished SS 304 stems ensure corrosion resistance and durability.
Handwheel or Seal Cap Interchangeable: Allows for customized operation.
Seat Disc Made of PTFE (Taflon-No Lead): Resists wear and chemical corrosion for longer life.
Ball Bearing Seat Swivel: Enables smooth, low-friction operation.
Dirt-Resistant Taper (Conical) Seat: Prevents debris buildup, maintaining performance integrity.
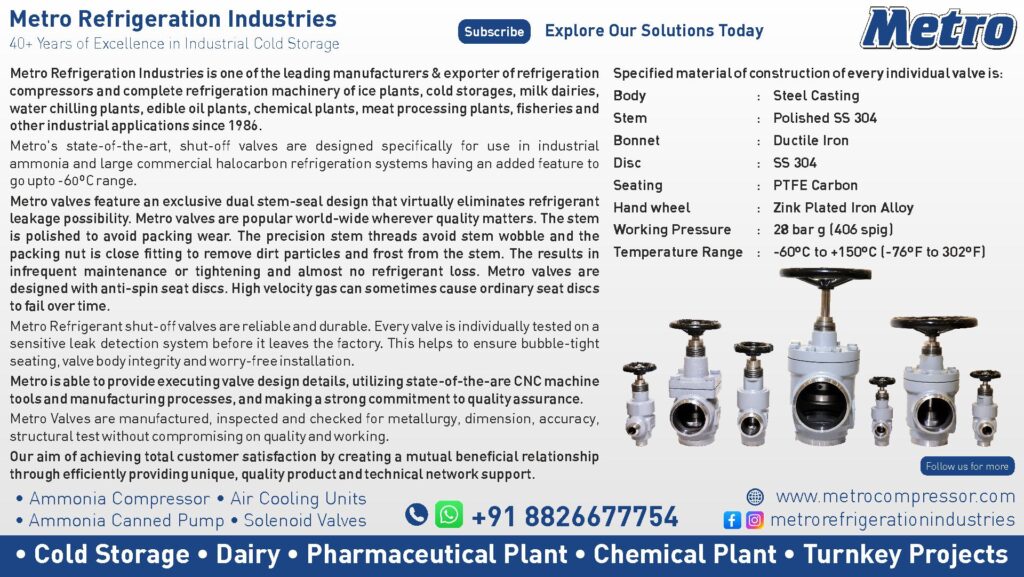
Ammonia Valve Specifications
Body: Steel Casting
Stem: Polished SS 304
Bonnet: Ductile Iron
Disc: SS 304
Seating: PTFE Carbon
Handwheel: Zinc-Plated Iron Alloy
Working Pressure: Up to 28 bar g (406 psig)
Temperature Range: -60°C to +150°C (-76°F to 302°F)
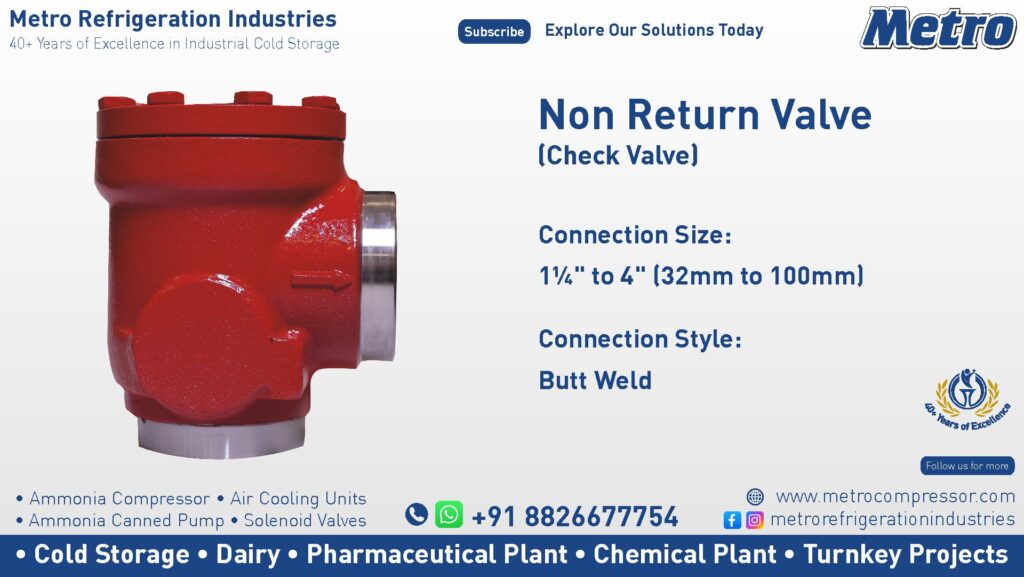
Types of Ammonia Valves
Ammonia Shut-Off Valves: For isolating sections of the system during maintenance.
Ammonia Solenoid Valves: Electrically operated for automated control.
Ammonia Angle Valves: Efficient design for directional flow.
Ammonia Ball Valves: Full-bore operation for high flow capacity.
Ammonia Check Valves: Prevents backflow in refrigeration systems.
Ammonia Globe Valves: Precise control of flow and pressure.
Ammonia Pressure Relief Valves: Ensures system safety by releasing excess pressure.
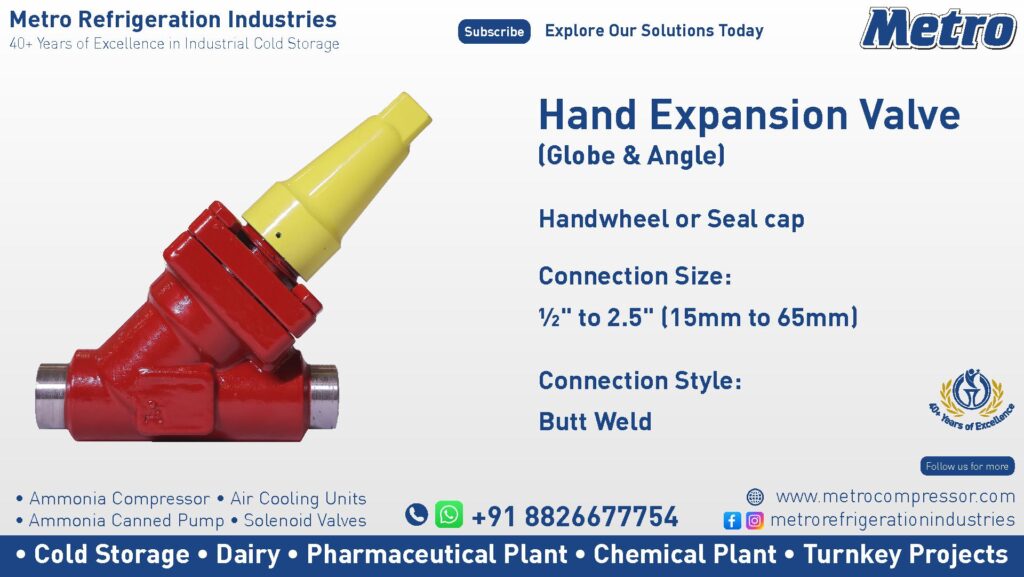
Applications of Ammonia Refrigeration Valves
Ammonia valves are indispensable across industries due to their versatility and durability:
1. Cold Storage Facilities
Maintain the right temperature for perishable goods like fruits, vegetables, meat, and seafood.
2. Food Processing
Support freezing, chilling, and maintaining production lines with hygienic conditions.
3. Pharmaceuticals
Crucial for temperature-sensitive storage, including vaccines and medicines.
4. Chemical Manufacturing
Enable precise temperature control for chemical reactions and processes.
5. Ice Plants
Efficient ice production and storage for industrial and commercial uses.
6. Breweries and Distilleries
Regulate temperatures for fermentation and storage processes.
7. Industrial Ammonia Refrigeration Systems
Critical for cooling machinery and maintaining operational environments.
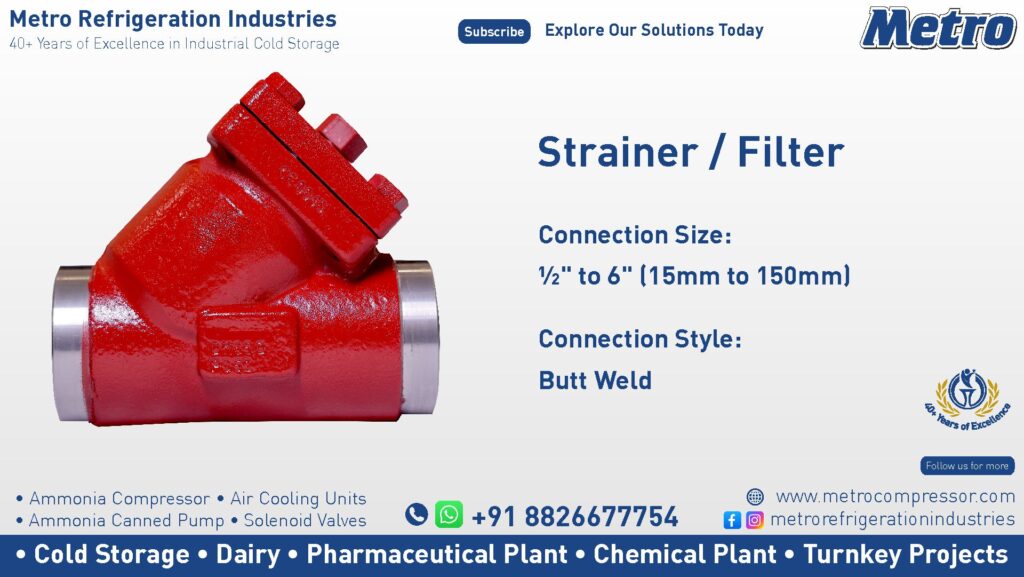
Metro Refrigeration Industries: A Comprehensive Product Line
Complete Product Line
Our advanced product line includes:
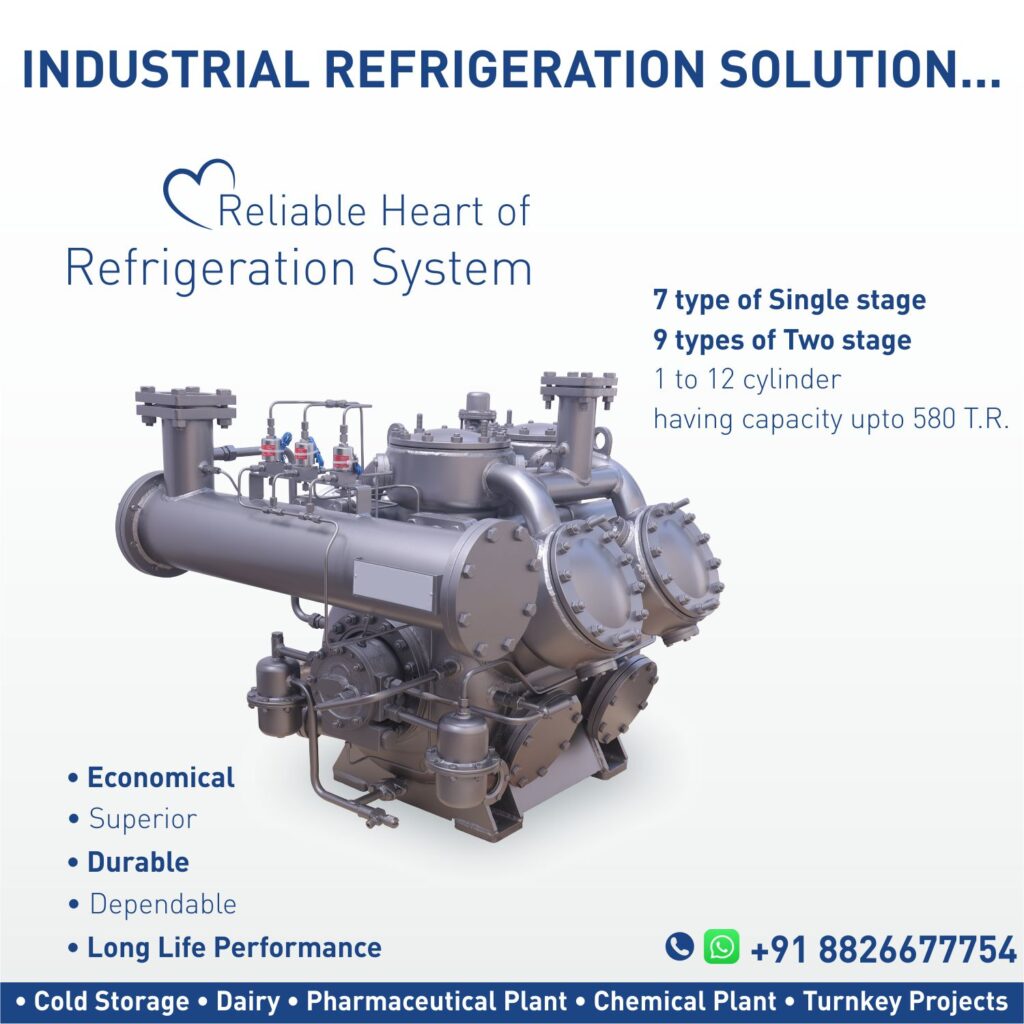
Ammonia Compressor: Backbone of Industrial Ammonia Refrigeration System
Our Nh3 refrigeration compressor are designed to deliver unmatched performance, ensuring reliability and efficiency across a wide range of applications. The range includes:
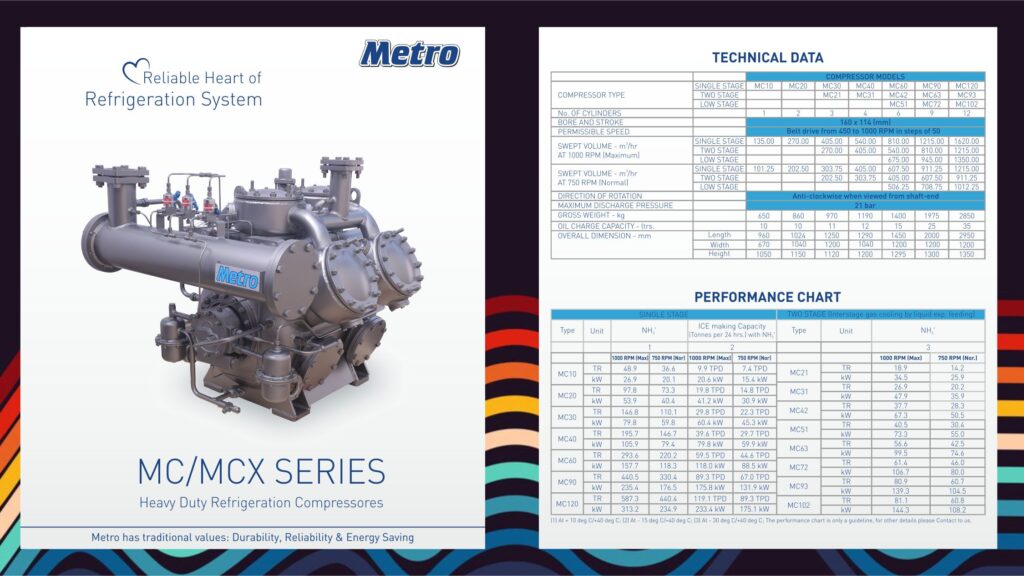
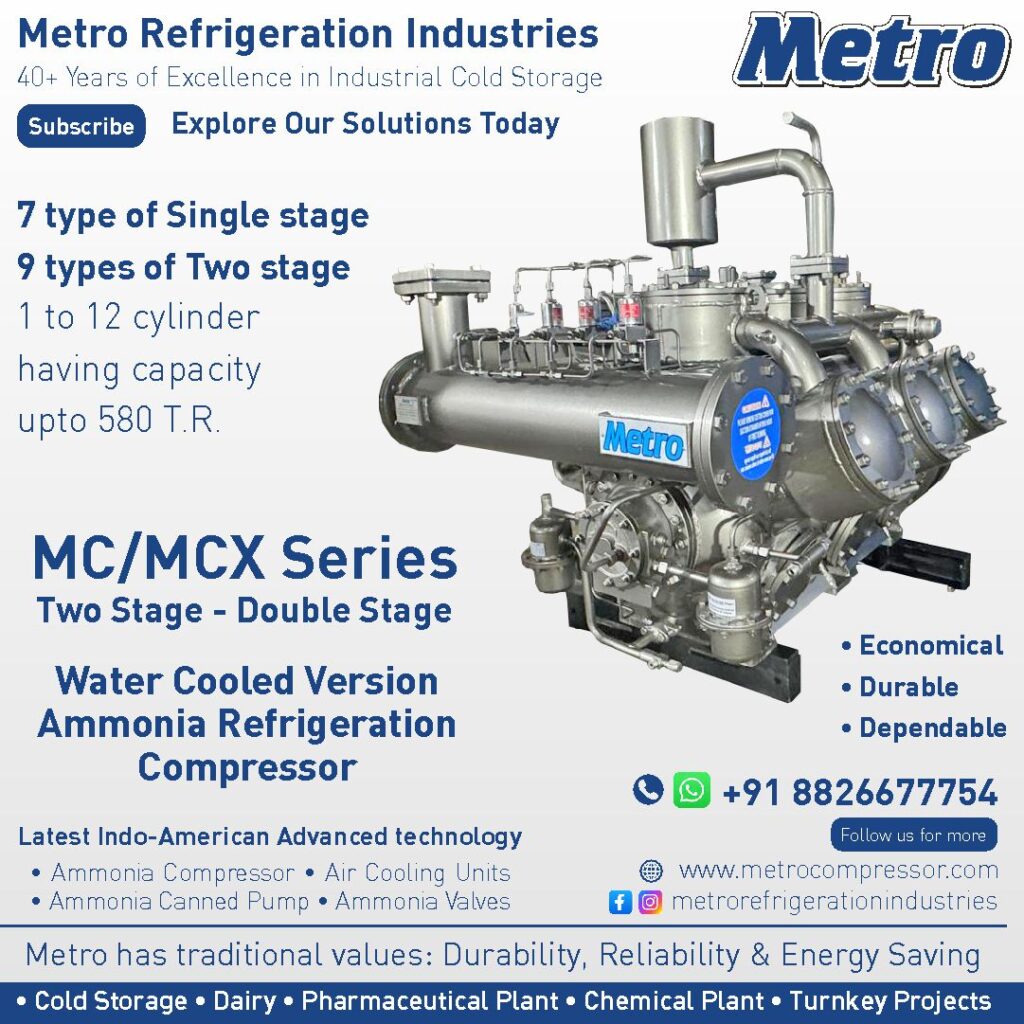
- MC Series (Water Cooled Nh3 Compressor): Ideal for industries requiring consistent cooling under extreme conditions.
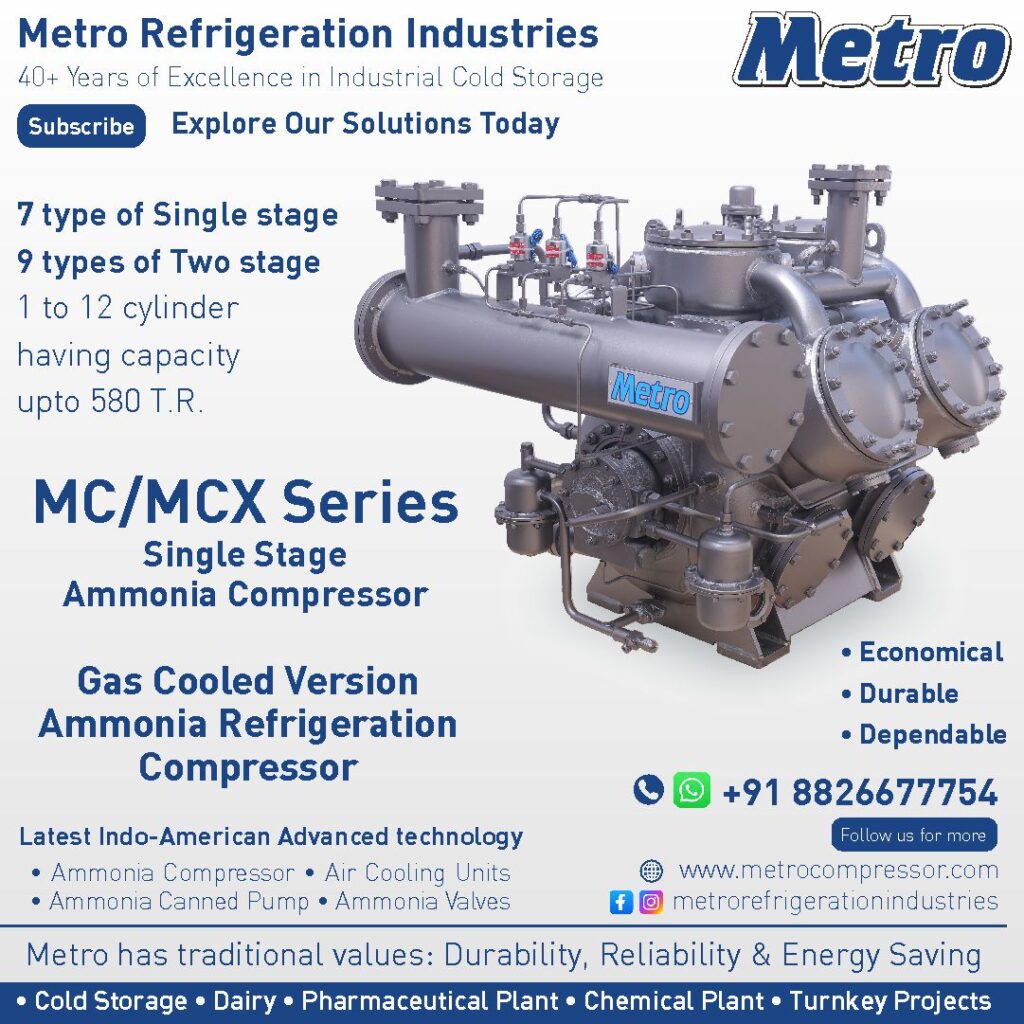
- MCX Series (Gas Cooled Nh3 Compressor): Designed for energy-efficient operation in diverse environments.
Comprehensive Range of Nh3 Compressor
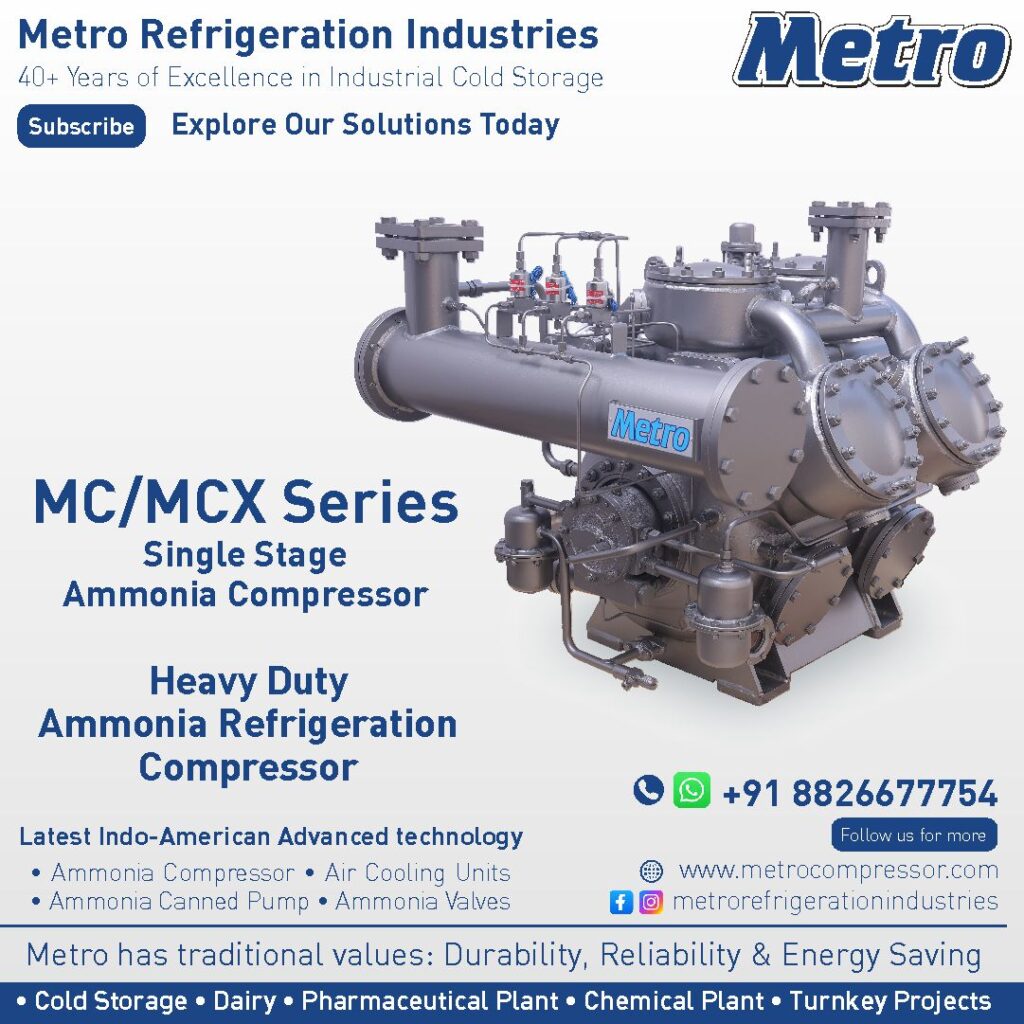
- Single Stage Ammonia Compressor: Available in 7 types, featuring 1 to 12 cylinders with capacities up to 580 T.R. These refrigeration compressor are perfect for moderate refrigeration requirements.
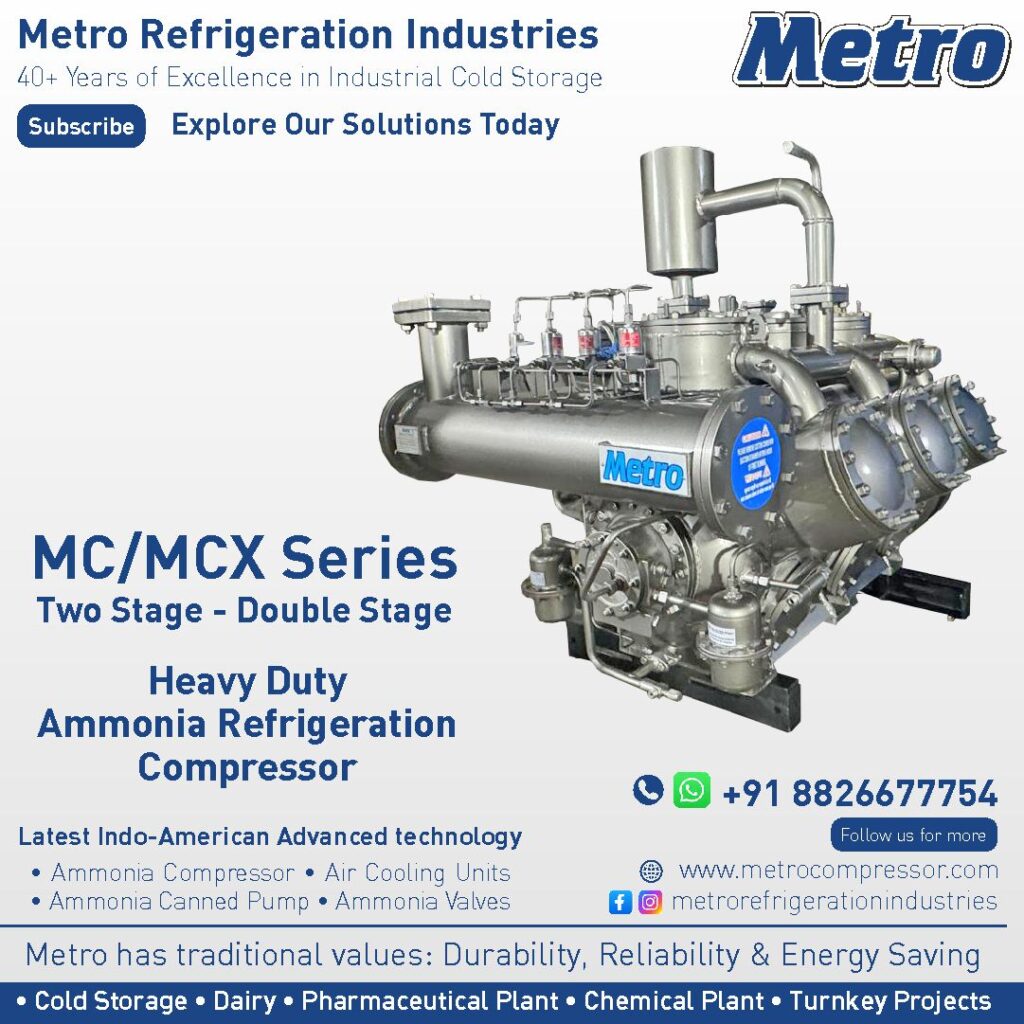
- Two Stage Ammonia Compressor (Compound Version): Available in 9 types, featuring 1 to 12 cylinders with capacities up to 580 T.R. Engineered for applications requiring precise temperature control at low and ultra-low temperatures.
Additional Equipment and Solutions
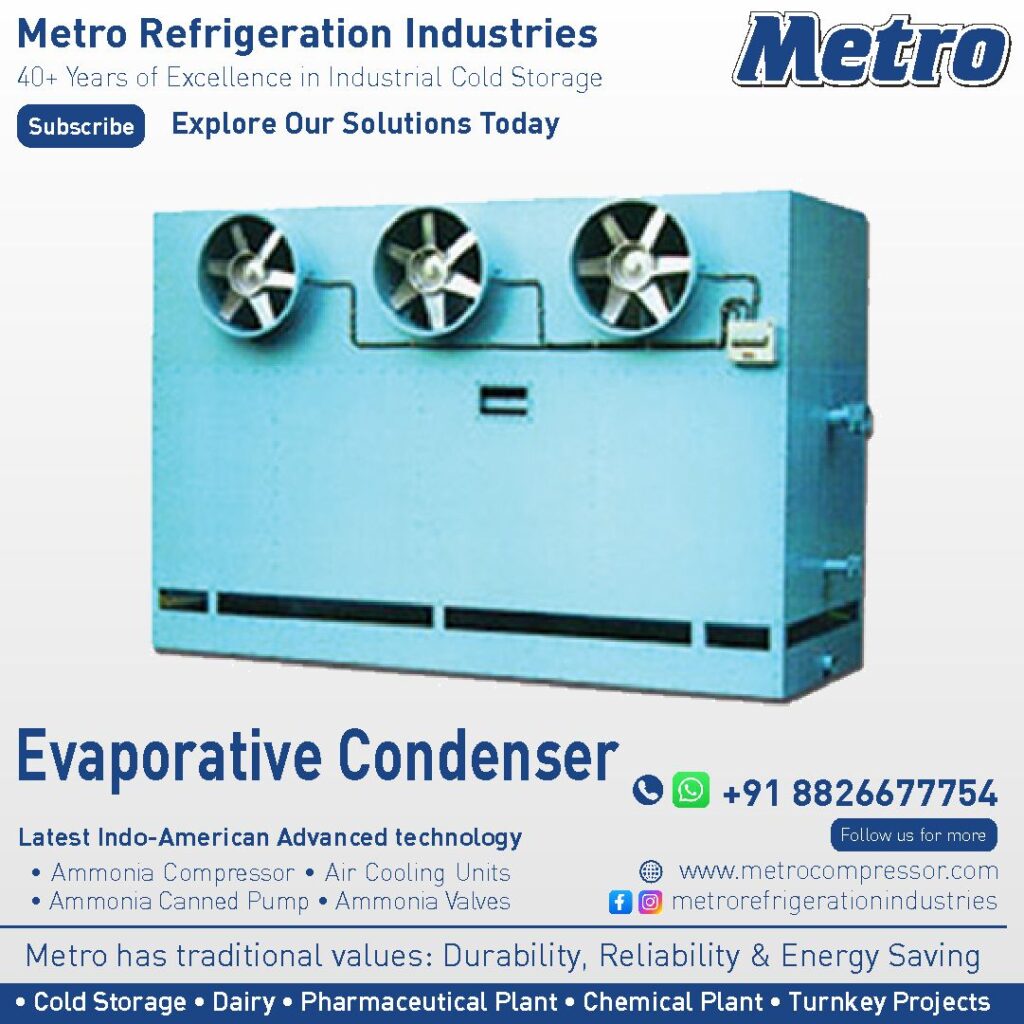
- Evaporative Condenser: Engineered for maximum heat transfer and reduced energy consumption in refrigeration systems.
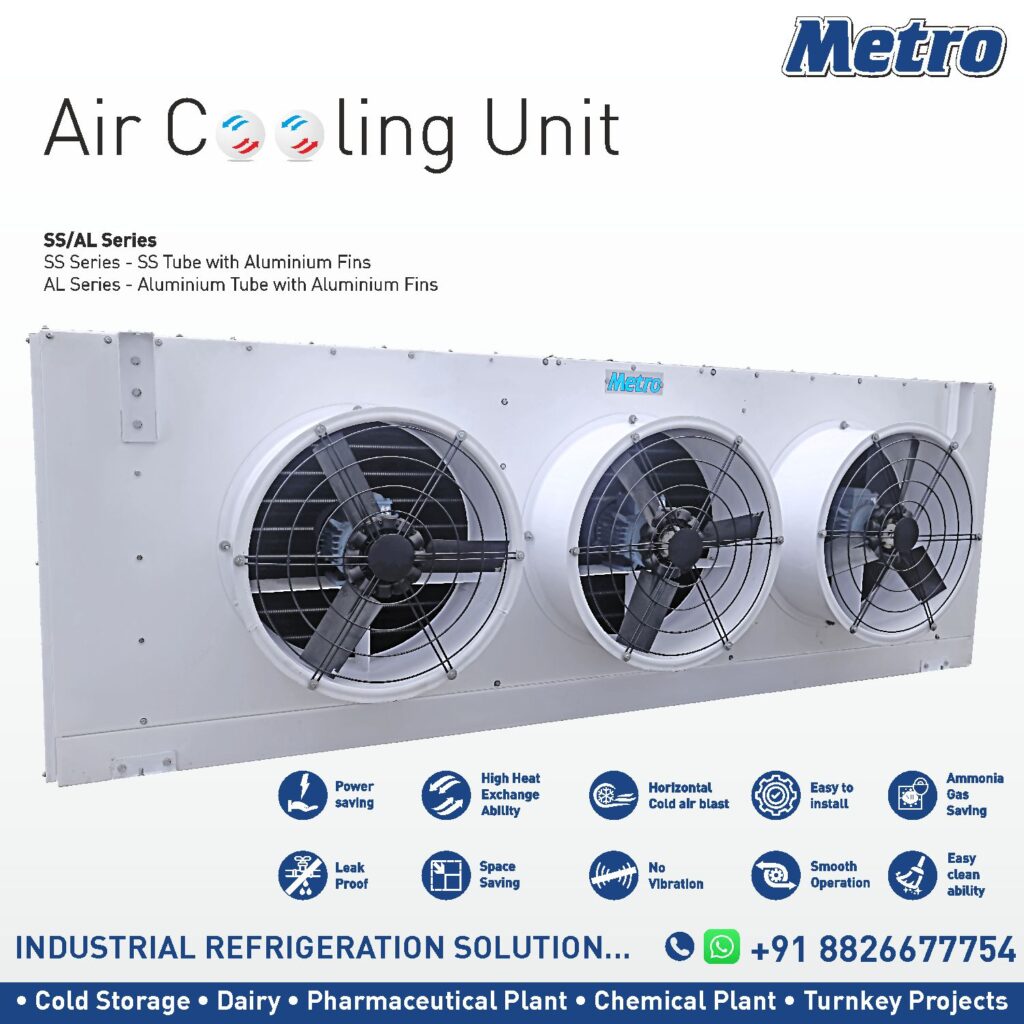
- Air Cooling Units: SS and AL Series durable and efficient cooling solutions, including stainless steel and aluminum options.
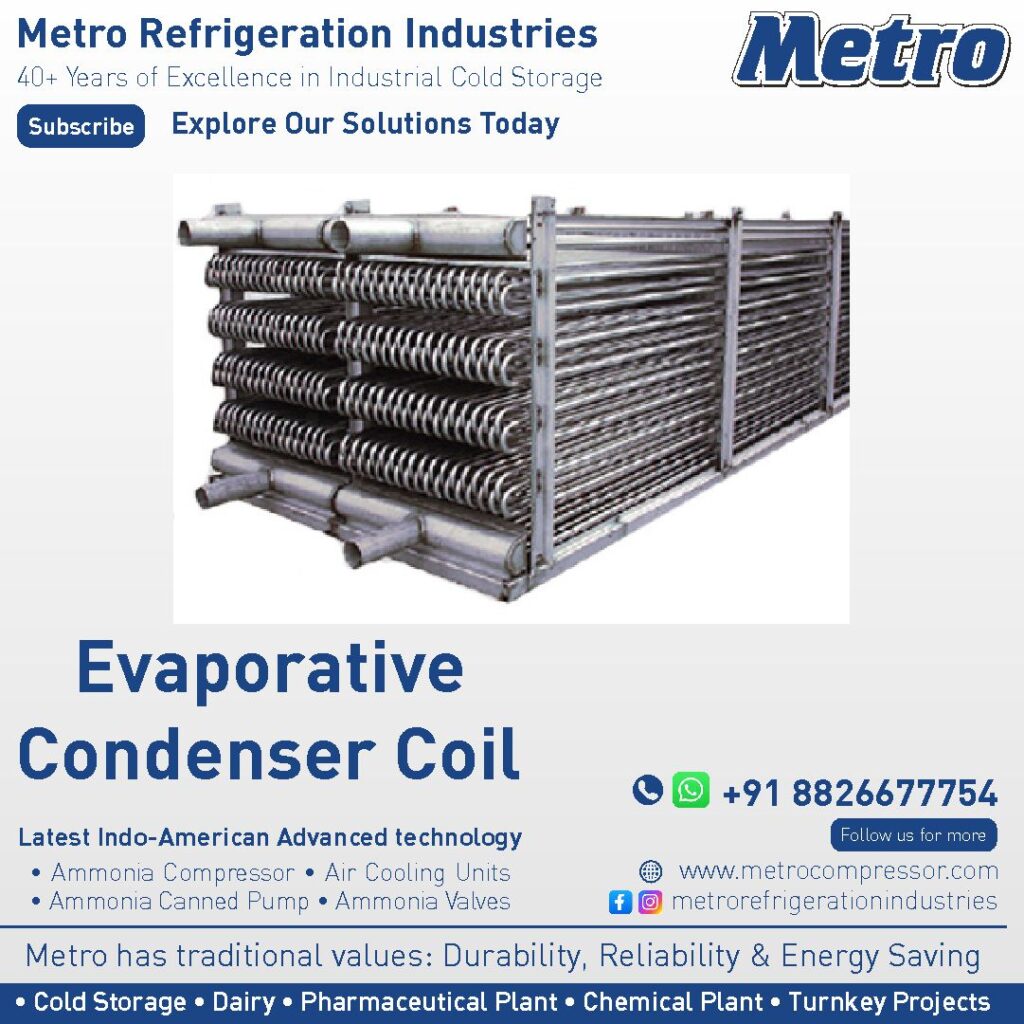
- Evaporator Coils: Ensure consistent cooling performance with our advanced ammonia evaporator coils.
- Ammonia Evaporative Coolers: Energy-saving Nh3 cooling systems for industrial applications.
- Cooling Coil Units: Maintain temperature precision with our high-performance cooling coil units.
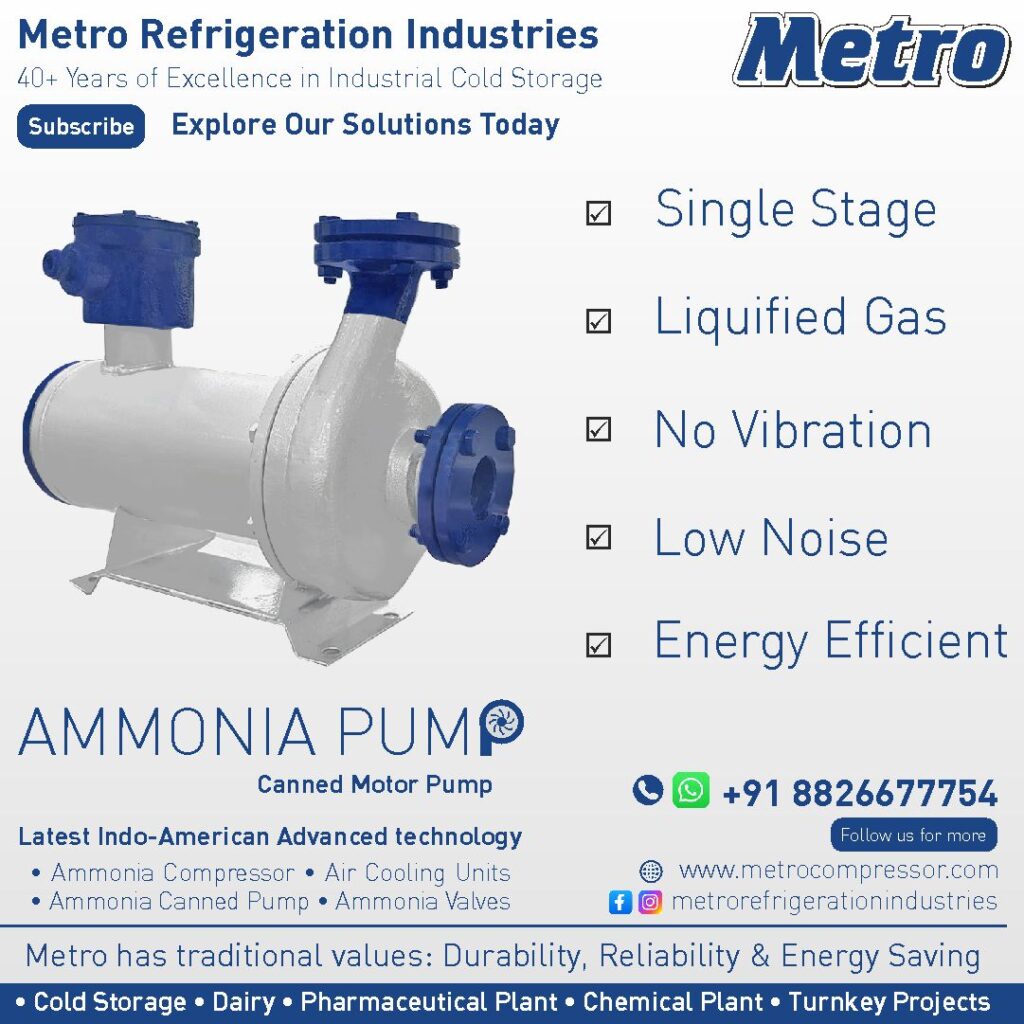
- Ammonia Canned Pumps: Built for reliable ammonia transfer in industrial refrigeration systems.
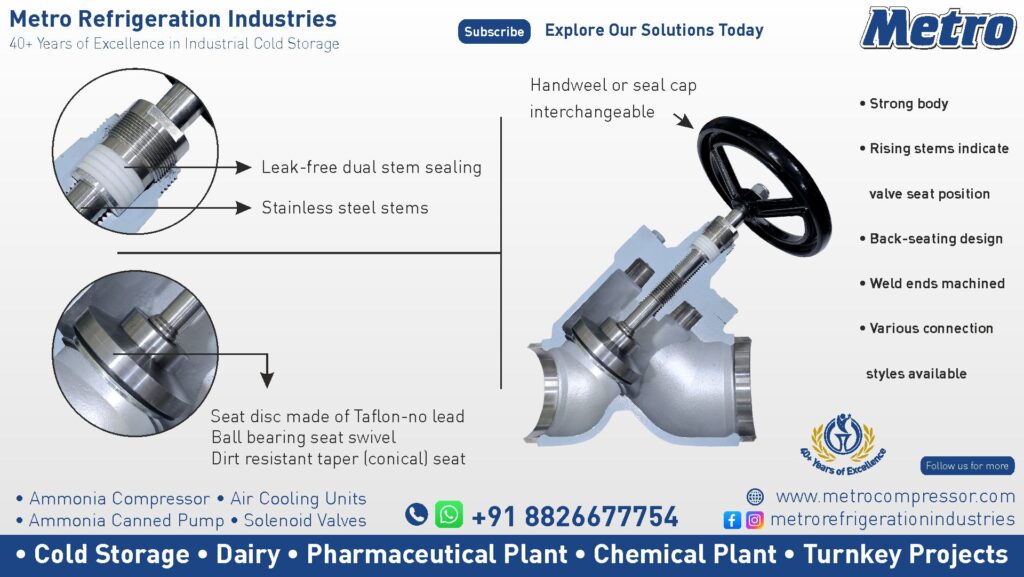
- Ammonia Valves: Precision-engineered valves for safe and efficient ammonia flow control.
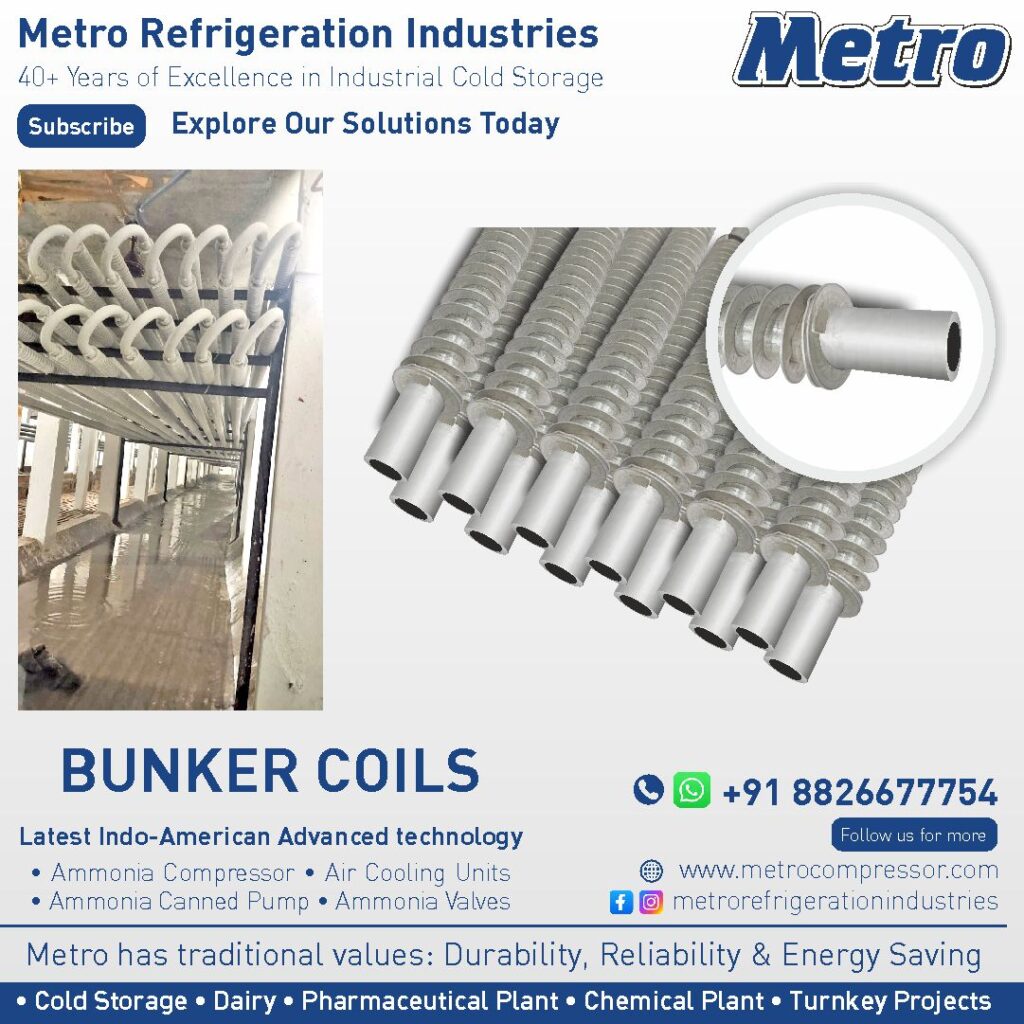
- Bunker Coils: High-efficiency heat transfer coils for industrial refrigeration processes.
- LPR & HPR: Optimize refrigeration system performance with low pressure receivers and high pressure receivers.
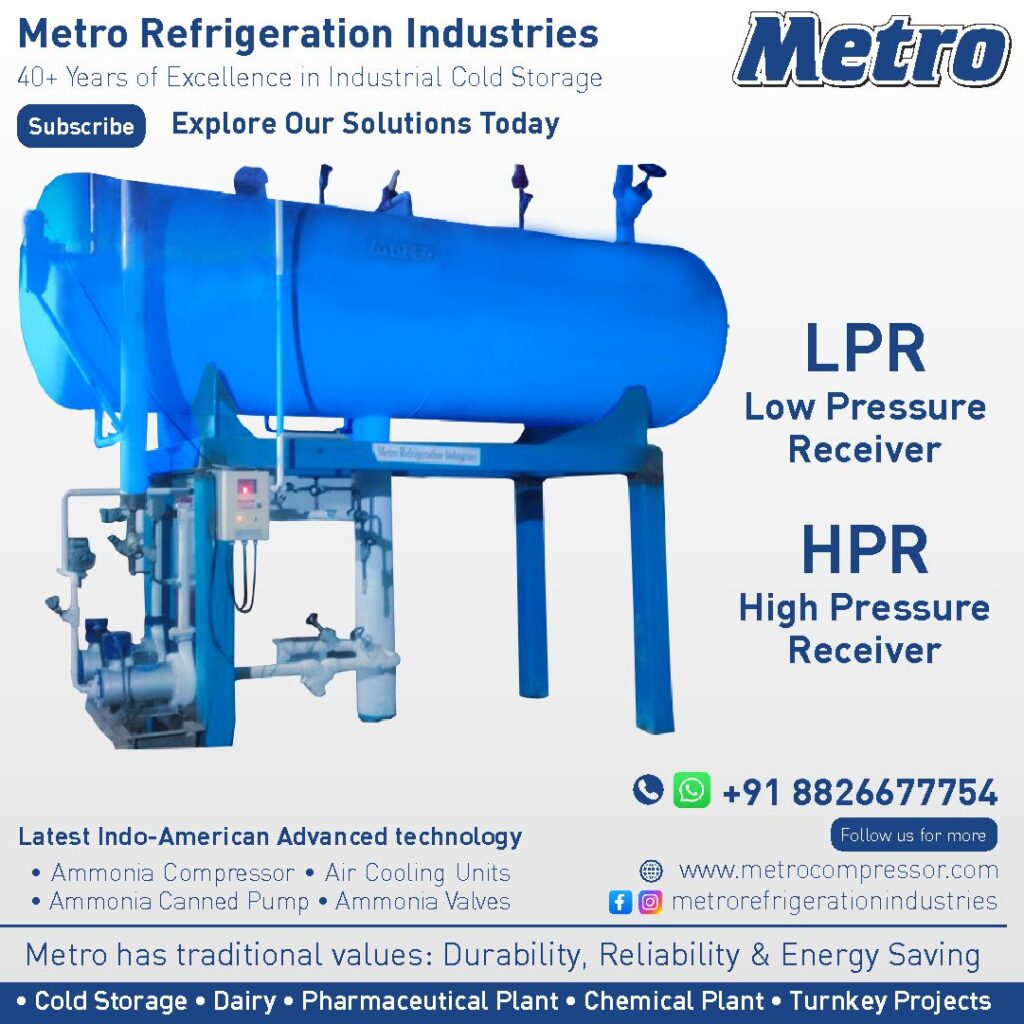
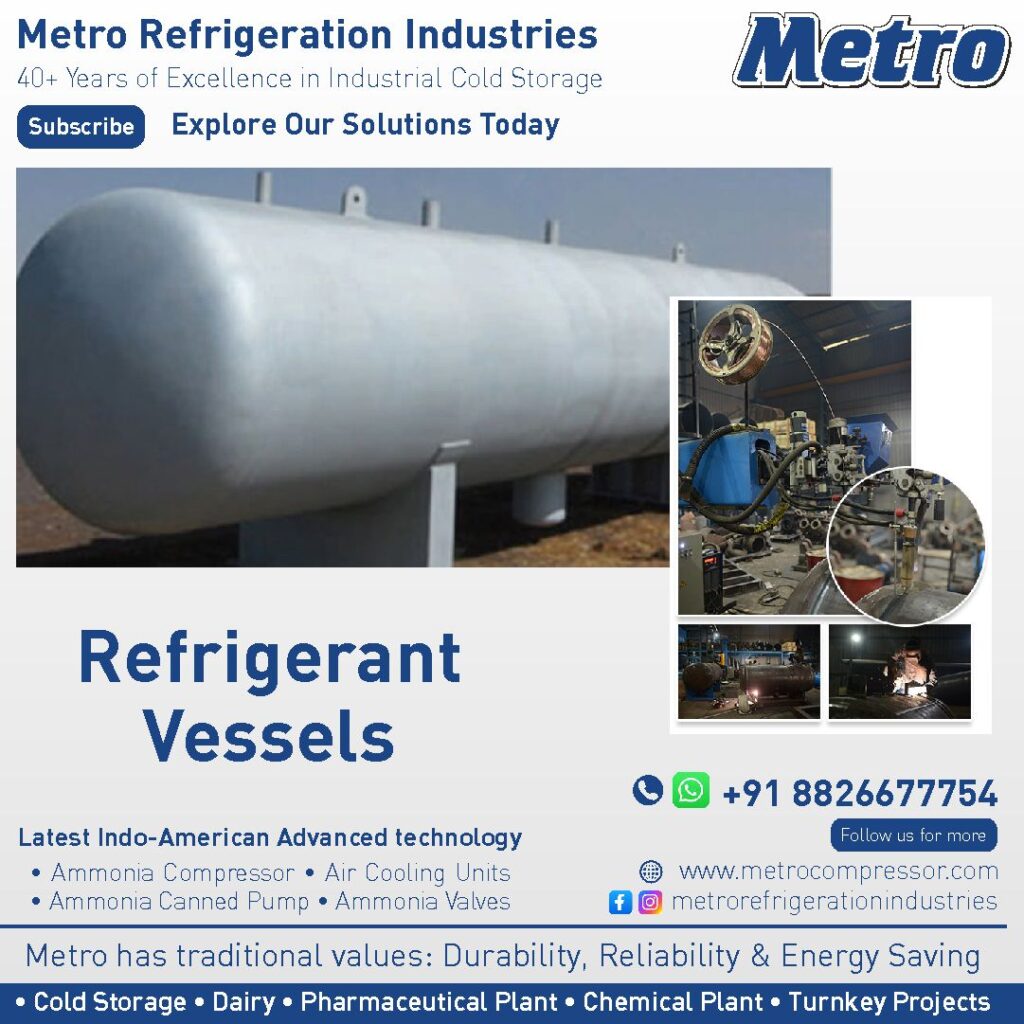
- Refrigerant Vessels: Secure and efficient refrigerant storage solutions for industrial use.
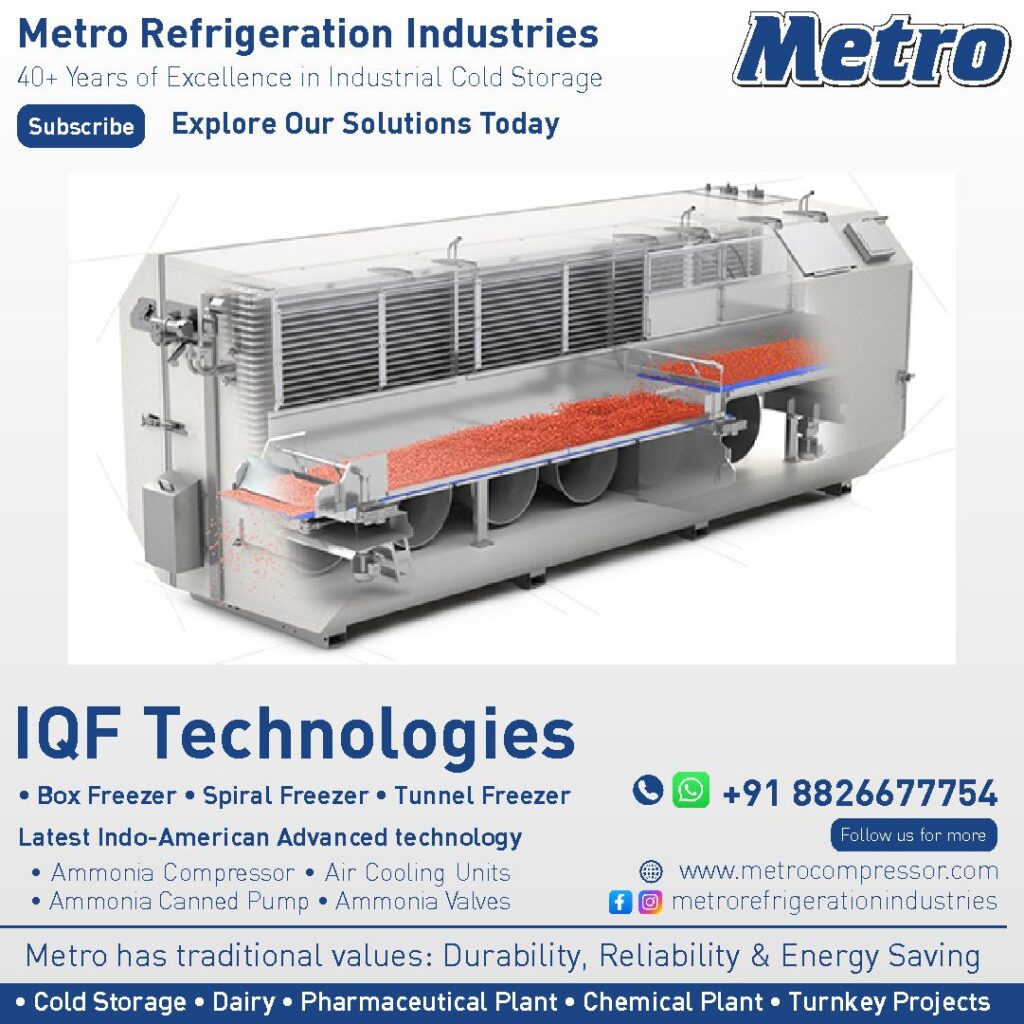
- IQF Technology: Advanced freezing technology to preserve food quality and extend shelf life.
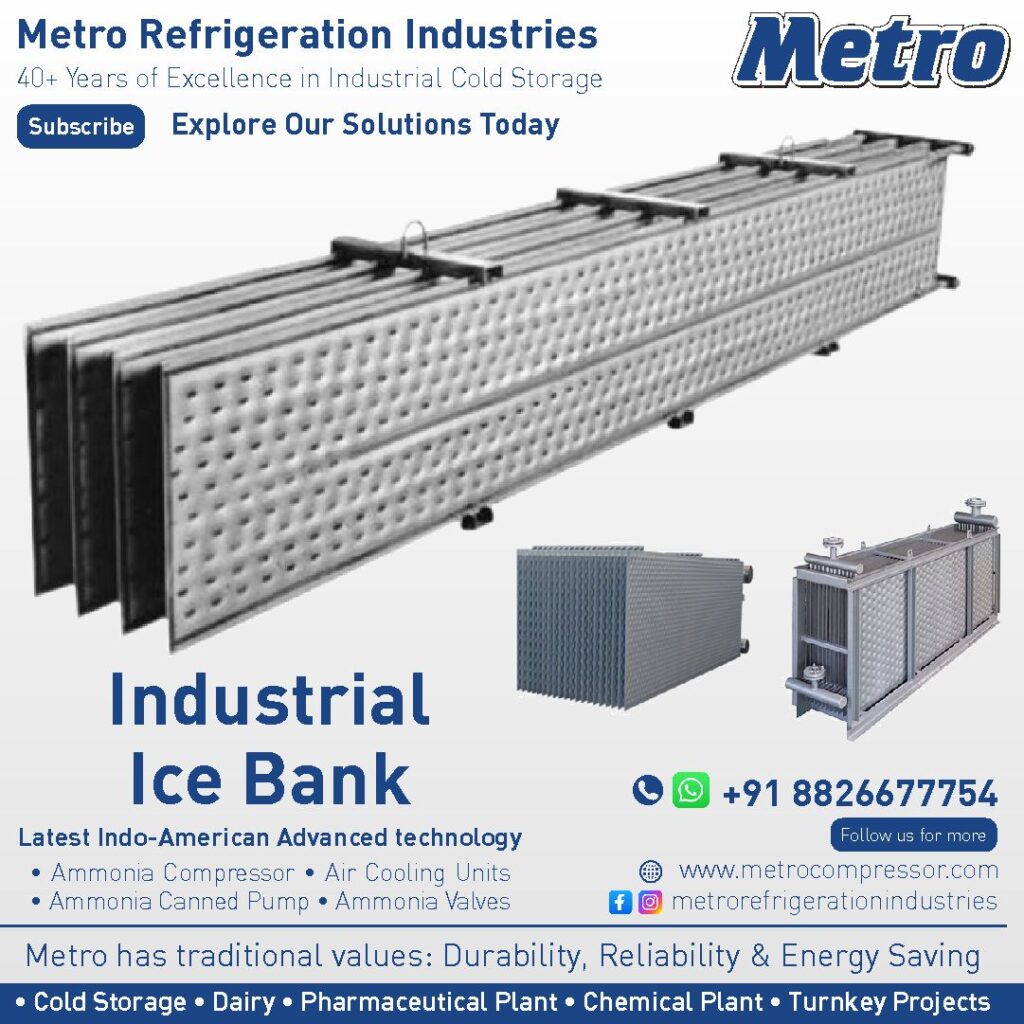
- Industrial Ice Bank: Dependable ice storage systems for industrial cooling needs.
- Pillow Plates: Effective heat exchange solutions for refrigeration and industrial applications.
- Axial Fans: Improve airflow and cooling performance with durable axial fans.
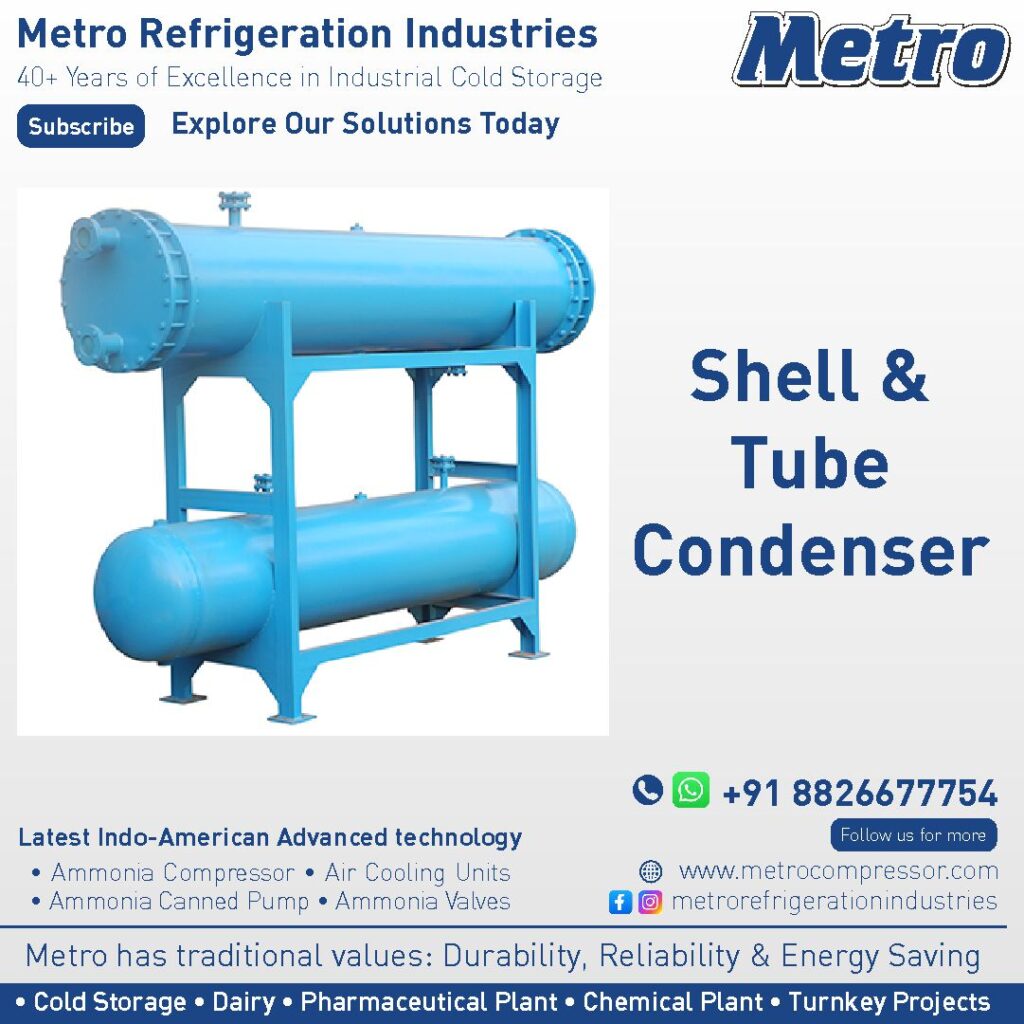
- Shell & Tube Condensers: Robust condensers designed for high-capacity industrial refrigeration.
- Ammonia Compressor Components: Ensure optimal operation with precision-engineered ammonia refrigeration compressor components.
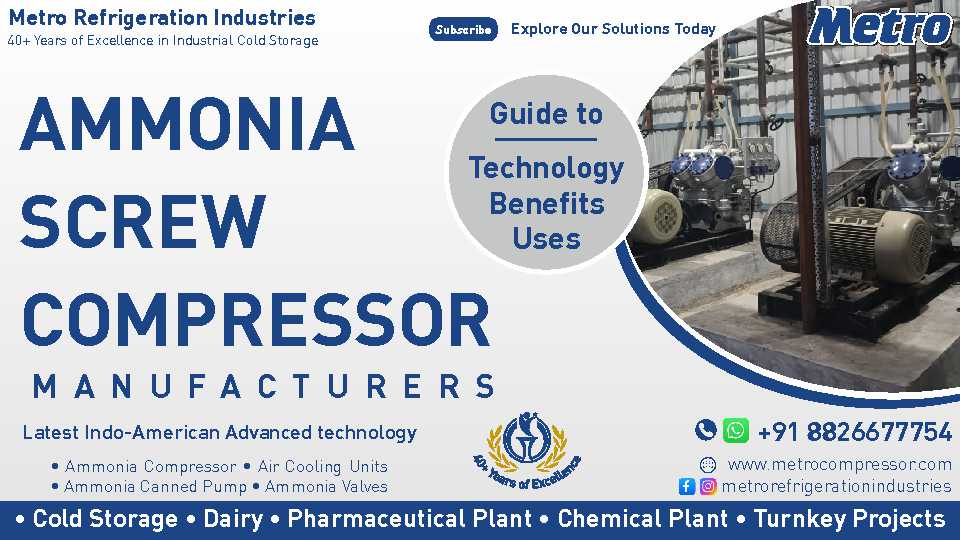
- Brine Chillers: Discover high performance ammonia brine refrigeration systems from leading brine chiller manufacturers. Our brine chiller plants, brine cooling systems, and brine refrigeration solutions ensure energy efficient industrial cooling. We also specialize in ammonia screw compressors and shell & tube condensers, delivering cost effective and reliable cooling solutions for various industries.
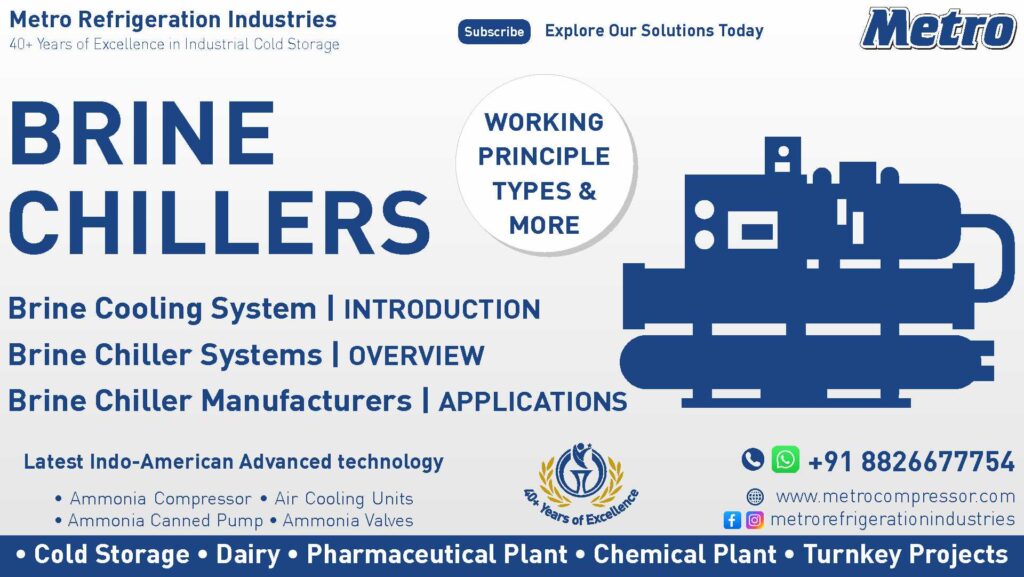
-
- Ammonia Compressor Components: Ensure optimal operation with precision-engineered ammonia refrigeration compressor components.

Why Choose Metro Refrigeration Industries?
Global Reach: Trusted by industries in over 30 nations, including Australia, UAE, and India.
Decades of Expertise: Over 40 years of delivering innovative and reliable solutions.
Prestigious Clients: Partnered with leading brands like Amul, Patanjali, and Adani.
Energy-Efficient Solutions: Designed to minimize costs and environmental impact.
Customizable Designs: Tailored to meet specific industrial needs.
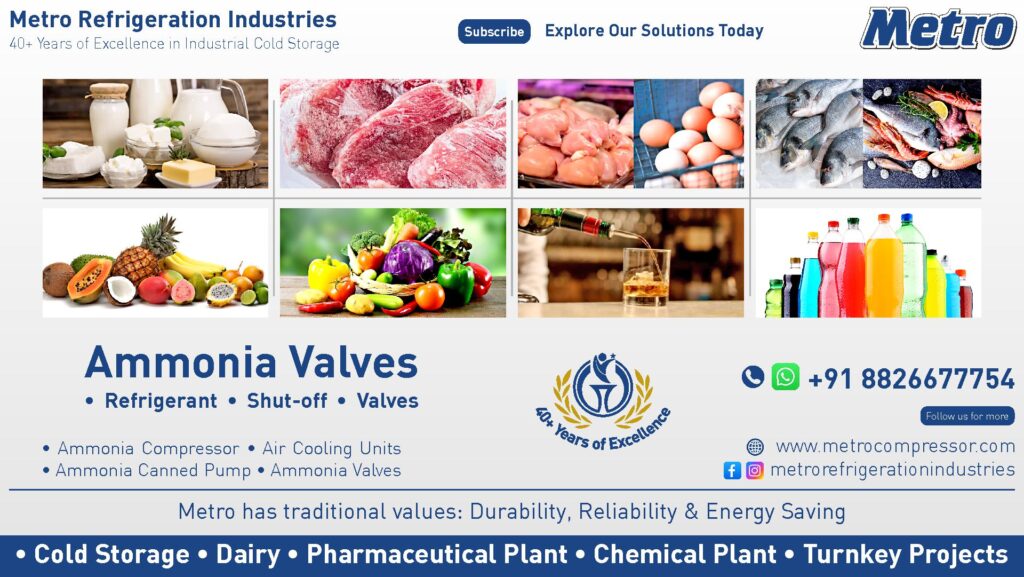
Conclusion
Ammonia valves are integral to the safety and efficiency of industrial refrigeration systems. At Metro Refrigeration Industries, we pride ourselves on delivering high-quality, durable, and precise valve solutions that meet the highest standards.
If you’re ready to optimize your ammonia refrigeration system, contact us today to explore our products and solutions.
If you’re looking for efficient, high-performance refrigeration systems for your industry, Metro Refrigeration Industries is the trusted partner. Reach out to us for solutions designed to save energy, reduce operational costs, and ensure precise temperature control across your facilities.
Contact Metro Refrigeration Industries
To explore our products and solutions for your refrigeration unit, get in touch:
Location: D-35, Meerut Road Industrial Area, Ghaziabad, Uttar Pradesh – 201 003, INDIA
Email: sales@metrorpl.com
Phone: +91-120-2712176, 2752030, 2757568, 2757269, 2713759
Customer Care: +91 88266 77754
Website: www.metrocompressor.com
Explore more related blogs:
Meat Processing Plant
We specialize in manufacturing cutting-edge refrigeration solutions for meat processing plants, catering to beef, chicken, cattle, seafood, fish, prawns, crabs, and frozen chicken. Our advanced systems ensure precise temperature control, freshness, and quality preservation. Trusted by industries for energy efficiency and durability, we provide comprehensive solutions tailored to meet diverse processing needs.
Onion Cold Storage
Ice Bank Refrigeration System
Air Cooling Units
Ice Bank Tank
Cold Storage Business Guide
Ammonia Refrigeration System
CA Cold Storage
Controlled Atmosphere Cold Storage
Apple Cold Storage
CA Cold Storage Chambers
IQF Technology
Ice Bank Chiller System
Individual Quick Frozen Technology
Blast Freezers
Blast Chillers
Curd Blast Rooms
Curd Incubation Room
Curd Incubation Chamber
Dairy Processing Plant
Cold Storage Explained
Ammonia Evaporators
Air Cooling Evaporators
Evaporators
Evaporative Condenser
Cooling Coils
Ammonia Cooling Coils
Ammonia Evaporative Condenser
Ammonia Air Cooling Units