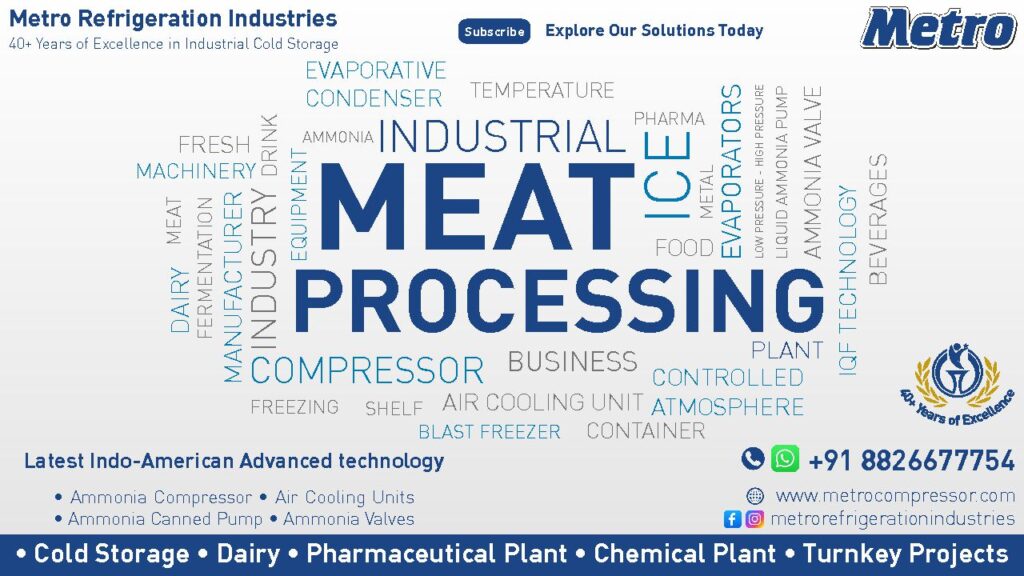
A Complete Guide to Setting Up a Meat Processing Unit: Requirements, Steps, and Best Practices
The meat processing industry plays a vital role in the global food supply chain, ensuring that meat products are safely and efficiently processed for both local and international markets. Whether it’s beef, pork, poultry, or seafood, modern meat plants are equipped to handle a wide range of meats with specialized designs and machinery.
In this guide, we will cover the types of meat processing units, their layouts, associated costs, and how specialized facilities cater to specific meat types, including beef, pork, poultry, chicken, lamb, deer, and seafood processing.
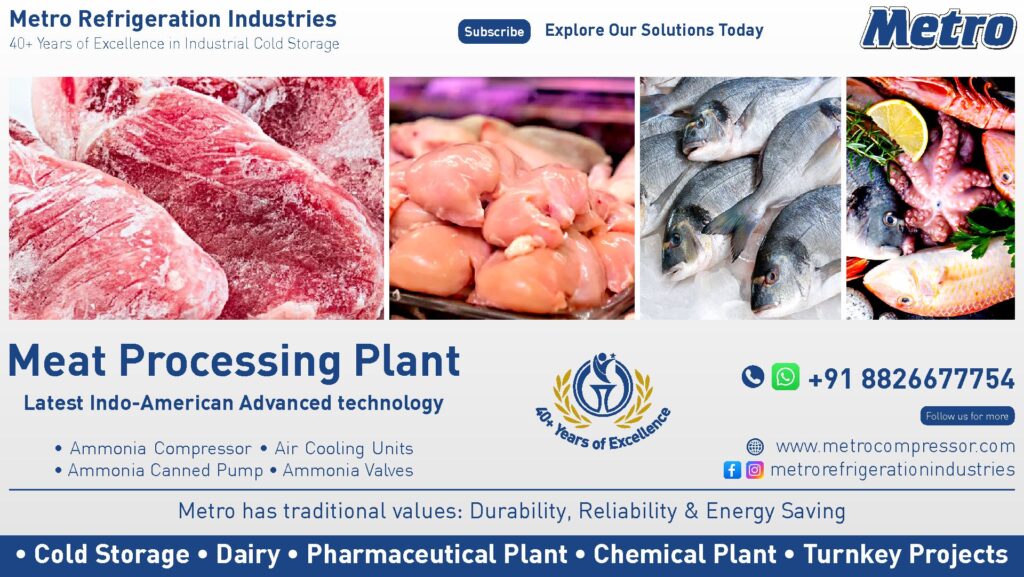
What Is a Meat Processing Plant?
A meat processing unit is a facility where raw meat is processed into finished products like packaged cuts, sausages, ground meat, and even specialty items. These plants utilize advanced technology and equipment to ensure hygiene, safety, and efficiency in meat handling.
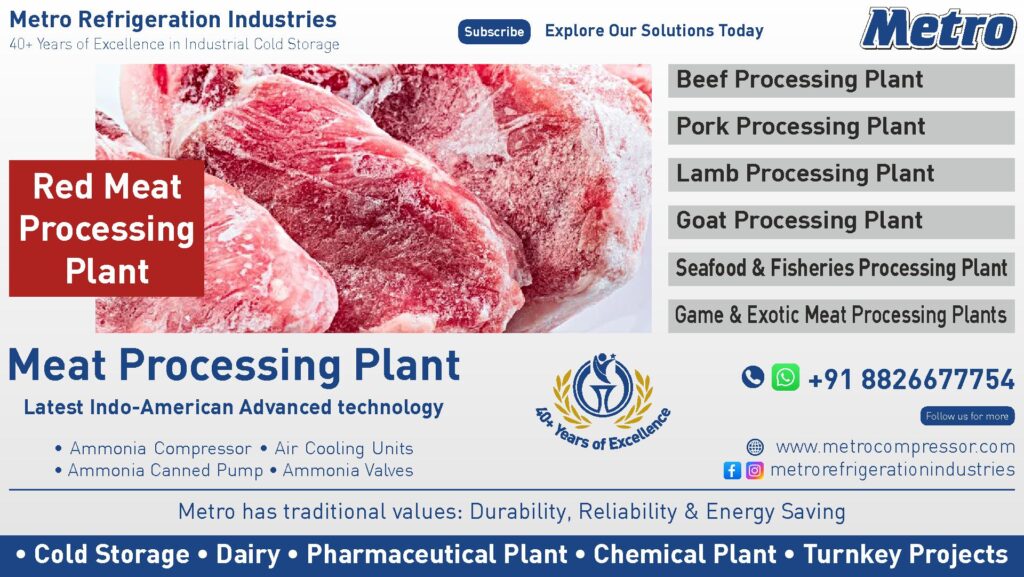
Types of Meat Processing Plants
Each type of meat processing unit is designed to meet the specific requirements of different meat categories. The major types include:
1. Beef Processing Plants
- Handle cattle slaughter, cutting, deboning, and packaging.
- Often include facilities for beef processing plant design and cold storage integration.
- Key Features:
- Heavy-duty cutting machinery.
- Advanced refrigeration for carcass storage.
- Cryogenic freezing for export-grade beef products.
2. Pork Processing Plants
- Focus on processing pork into cuts, bacon, sausages, and ham.
- Key Features:
- Specialized curing and smoking units.
- Hygienic pork slaughtering systems.
- Custom cold storage for preservation.
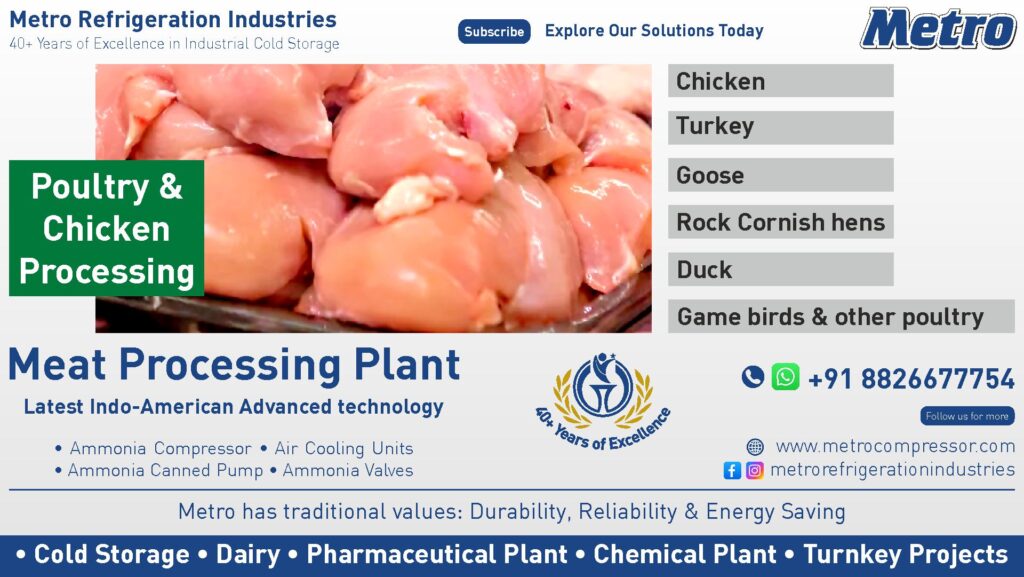
3. Poultry Processing Plants
- Cater to chicken, turkey, and other poultry meats.
- Key Features:
- Chicken plant chillers for rapid cooling after slaughter.
- Advanced equipment for cleaning, deboning, and packaging.
- IQF Technology (Individual Quick Freezing) for frozen chicken products.
4. Lamb and Goat Processing Plants
- Process lamb and goat meat into retail cuts, specialty products, and ground meat.
- Include sections for slaughter, carcass cooling, and packaging.
5. Game and Exotic Meat Processing Plants
- Handle deer, rabbit, and other game meats.
- Key Features:
- Precision cutting equipment.
- Super freezing technology for niche export markets.

6. Seafood and Fisheries Processing Plants
- Cater to fish, spawn, crabs, and other seafood.
- Specialized in cold storage for fish and flash-freezing techniques for quality preservation.
- Include CA cold storage and IQF systems for individual seafood items.
Why Is a Meat Processing Plant Important?
- Safety and Hygiene: Ensures all meats are processed under strict food safety protocols.
- Efficiency: Advanced machinery speeds up production while maintaining quality.
- Extended Shelf Life: Cold storage and freezing techniques prevent spoilage.
- Economic Growth: Contributes to local and international trade.
Meat Processing Plant Design and Layout
The design of a meat processing unit layout directly impacts efficiency and compliance. Important factors include:
- Separate Work Zones: Prevent contamination between raw and processed products.
- Temperature-Controlled Storage: Dedicated areas for carcass chilling and frozen storage.
- Specialized Areas for Each Meat Type: Separate sections for beef, pork, poultry, and seafood.
Metro Refrigeration Industries offers custom-designed meat processing unit layouts tailored to specific operational needs.
Equipment for Meat Processing Plants
Modern processing plants rely on cutting-edge machinery for optimal performance:
- Ammonia Compressors: Energy-efficient refrigeration solutions.
- Air Cooling Units: Maintain consistent temperatures for storage.
- IQF Technology: Freezes individual meat items quickly without clumping.
- Cryogenic Freezers: Ideal for rapid freezing of export-grade meats.
- Chicken Plant Chillers: Essential for poultry cooling immediately after processing.
- Cold Storage Systems: Include CA cold storage for meats and seafood.
Meat Processing Plant Costs
The cost to build a meat processing unit depends on factors like:
- Plant Size and Scale: Larger facilities cost more.
- Specialized Equipment: Advanced systems like super freezing or IQF technology increase investment.
- Custom Features: Integrating cold storage or seafood processing raises costs.
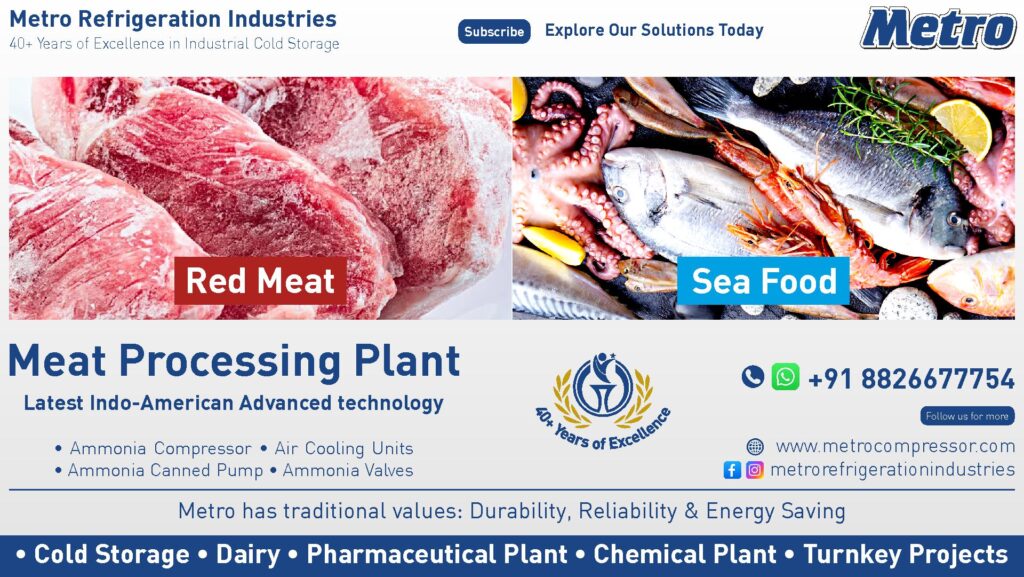
Examples:
- Beef Processing Plant Cost: Higher due to the size and weight of carcasses.
- Chicken Processing Plant Cost: Relatively lower but depends on the inclusion of chillers and freezers.
- Seafood Processing Costs: Costs vary based on the freezing technology and storage requirements.
How to Start a Meat Processing Plant Business
- Develop a Business Plan: Identify your target market (e.g., beef, poultry, seafood).
- Secure Funding: Determine costs, including land, equipment, and operational expenses.
- Partner with Experts: Collaborate with Metro Refrigeration Industries for plant design and equipment supply.
- Comply with Regulations: Obtain necessary food safety certifications.
- Install Machinery: Invest in advanced equipment like chillers, freezers, and IQF systems.
Benefits of Modern Meat Processing Plants
- Improved Quality Control: Ensures fresh and safe products.
- Energy Efficiency: Advanced refrigeration systems reduce operational costs.
- Market Expansion: Supports export of high-quality products.
- Reduced Wastage: Efficient processes minimize waste and spoilage.
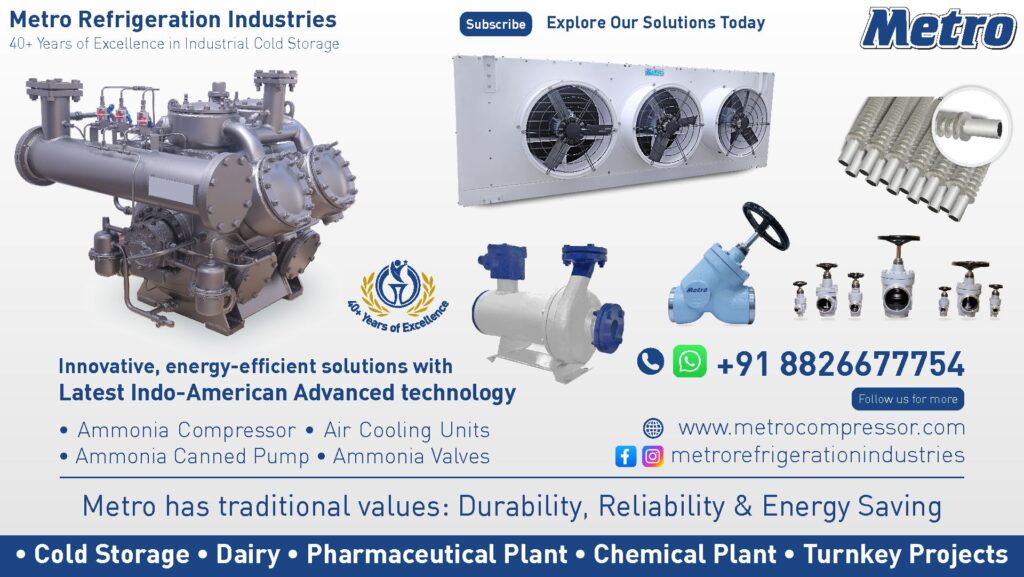
Metro Refrigeration Industries: Your Partner in Success
As a leading manufacturer in India, Metro Refrigeration Industries provides:
- Turnkey Solutions: Custom-built meat and seafood processing facilities.
- Advanced Technology: Indo-American systems for energy efficiency and performance.
- Comprehensive Equipment Range:
Common Questions About Meat Processing Plants
- What is the cost of a poultry processing plant?
Costs vary based on size and equipment but typically range from medium to high investment. - Can I process multiple meat types in one plant?
Yes, with separate zones and specialized equipment. - What is the role of CA cold storage in seafood processing?
It extends the shelf life by controlling atmospheric conditions.
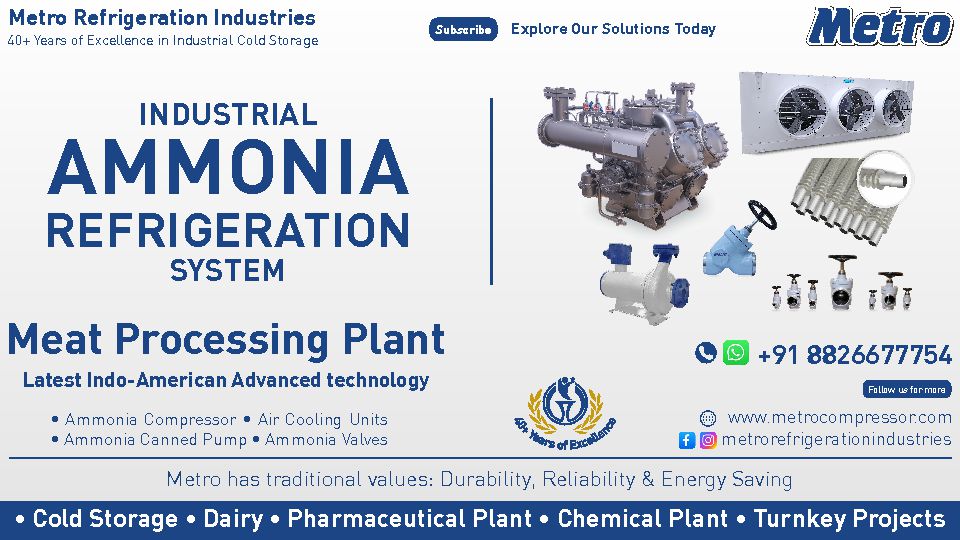
What is the role of refrigeration system in meat processing plant?
Refrigeration systems play a crucial role in meat processing by ensuring the preservation and safety of meat products throughout the production, storage, and distribution stages. Here are the key roles of refrigeration systems in meat processing:
- Preservation of Freshness: Refrigeration helps maintain the quality of meat by slowing down bacterial growth and enzymatic processes that cause spoilage. It ensures that the meat remains fresh for longer periods.
- Temperature Control: Refrigeration systems provide precise temperature control, ensuring that meat is stored and transported at the optimal temperatures. This helps prevent the growth of harmful pathogens like Salmonella and E. coli, which thrive at higher temperatures.
- Extended Shelf Life: By keeping meat at the right temperature, refrigeration extends its shelf life, reducing waste and improving product availability in markets, thus benefiting both consumers and producers.
- Compliance with Health Regulations: Refrigeration is essential for meeting food safety standards and regulations. Proper temperature management is critical in avoiding contamination and ensuring the meat products are safe for consumption.
- Efficient Processing and Distribution: Refrigeration allows for the efficient processing and distribution of meat, particularly for large-scale operations. It ensures that processed meat, including cuts and prepared products, can be stored safely until they are ready for shipment or sale.
- Cold Chain Management: A well-maintained cold chain, supported by refrigeration systems, ensures that meat products are kept at the correct temperature throughout the entire supply chain, from slaughterhouses to retailers, preventing spoilage and ensuring meat quality is preserved from start to finish.
Metro Refrigeration Industries offers reliable refrigeration solutions, incorporating advanced Indo-American technology, to support the meat processing industry. With energy-efficient systems and precise temperature control, we help ensure that meat is safely processed, stored, and transported.
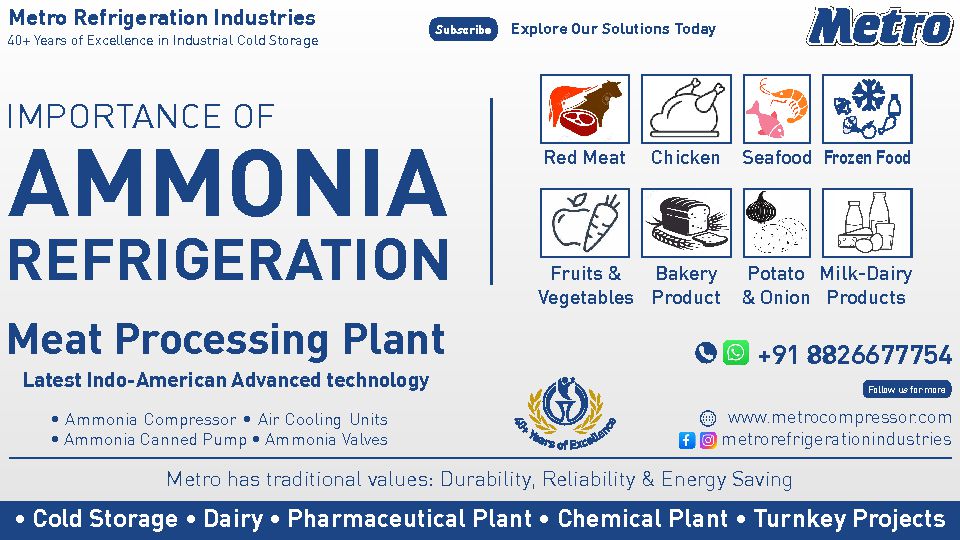
What is the importance of ammonia refrigeration in meat processing?
Ammonia refrigeration systems are highly important in meat processing due to their efficiency, cost-effectiveness, and environmental benefits. Here’s why ammonia plays a key role:
- Energy Efficiency: Ammonia has a high thermodynamic efficiency, meaning it can cool more effectively than many other refrigerants. This reduces energy consumption, leading to lower operational costs, which is crucial in large-scale meat processing facilities that require consistent and large-scale refrigeration.
- Powerful Cooling Capacity: Ammonia refrigeration systems are known for their powerful cooling capacity, making them ideal for maintaining the cold temperatures required in meat processing. These systems can rapidly cool large quantities of meat and help maintain the desired temperatures during both storage and transportation.
- Sustainability: Ammonia is a natural refrigerant, unlike synthetic refrigerants, which can contribute to environmental harm. It has zero ozone depletion potential and a low global warming potential, making it an eco-friendly option for meat processors who want to comply with sustainability goals and environmental regulations.
- Cost-Effectiveness: Ammonia is generally more affordable compared to other refrigerants, both in terms of initial investment and long-term operational costs. Its low cost makes it a popular choice for meat processing plants aiming to reduce energy and maintenance expenses.
- Safety and Reliability: When properly managed, ammonia refrigeration systems are safe and highly reliable. They have a long operational lifespan and require minimal maintenance, ensuring consistent temperature control throughout the meat processing and storage cycle.
- Consistency in Temperature Control: Ammonia refrigeration provides precise and reliable temperature control, which is critical in meat processing. Maintaining proper refrigeration temperatures prevents spoilage and bacterial growth, ensuring that meat remains safe, fresh, and high-quality.
- Improved Shelf Life and Quality: With ammonia refrigeration, meat products can be stored at the correct temperatures, extending their shelf life while maintaining their quality. This helps reduce waste and ensures the products remain fresh throughout the supply chain.
What refrigeration equipment and machinery is essential for a meat processing plant?
Refrigeration equipment is crucial in a meat processing unit to ensure optimal temperature control, product quality, and food safety throughout the processing, storage, and transportation stages. Here’s a list of essential refrigeration equipment commonly used in a meat processing unit:
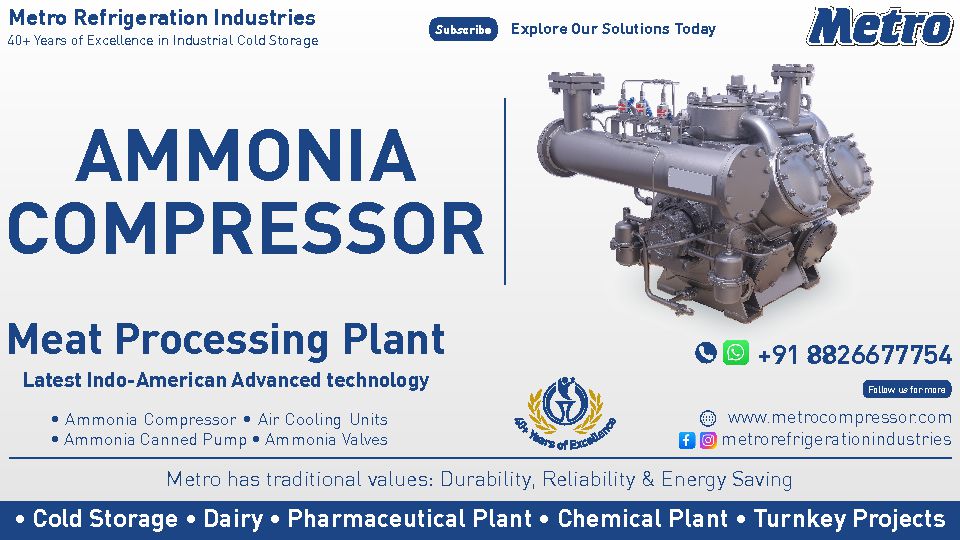
-
Ammonia Compressor
- Purpose: Drives the refrigeration process by compressing and circulating refrigerant gases.
- Applications: Essential for large-scale refrigeration systems in beef, poultry, and seafood plants.
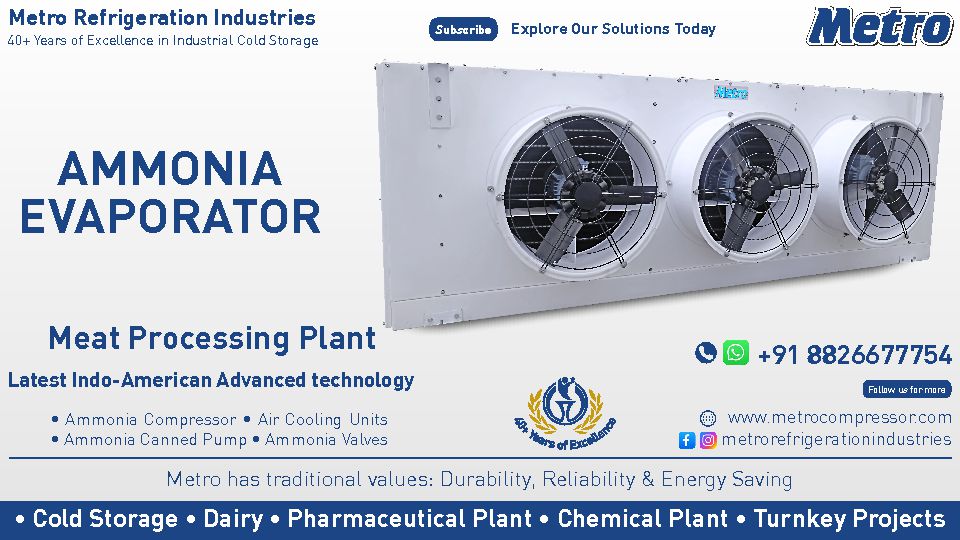
-
Evaporators
- Purpose: Removes heat from the processing environment or storage area.
- Applications: Used in meat processing unit refrigeration systems for chilling and freezing.
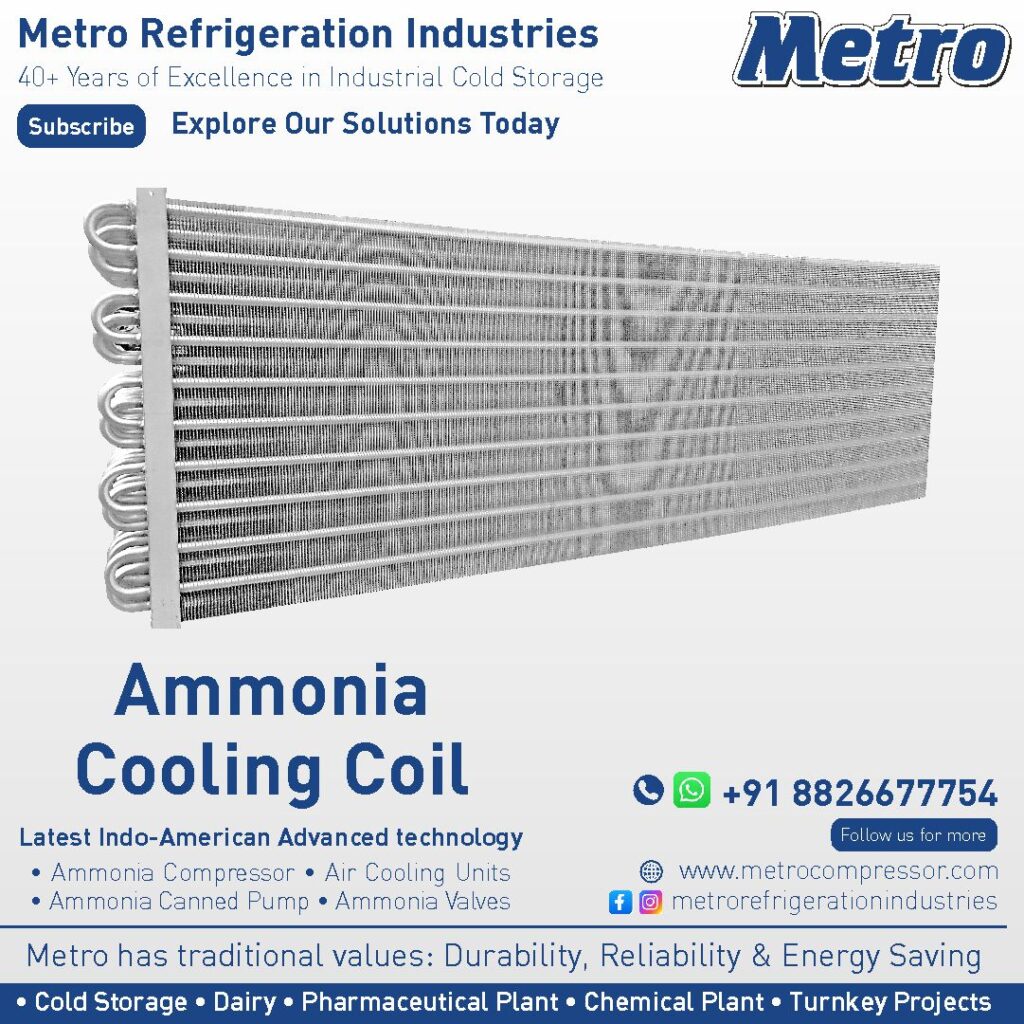
-
Cooling Coils
- Purpose: Transfers heat from the air to the refrigerant to maintain low temperatures.
- Applications: Found in chiller rooms and cold storage areas.
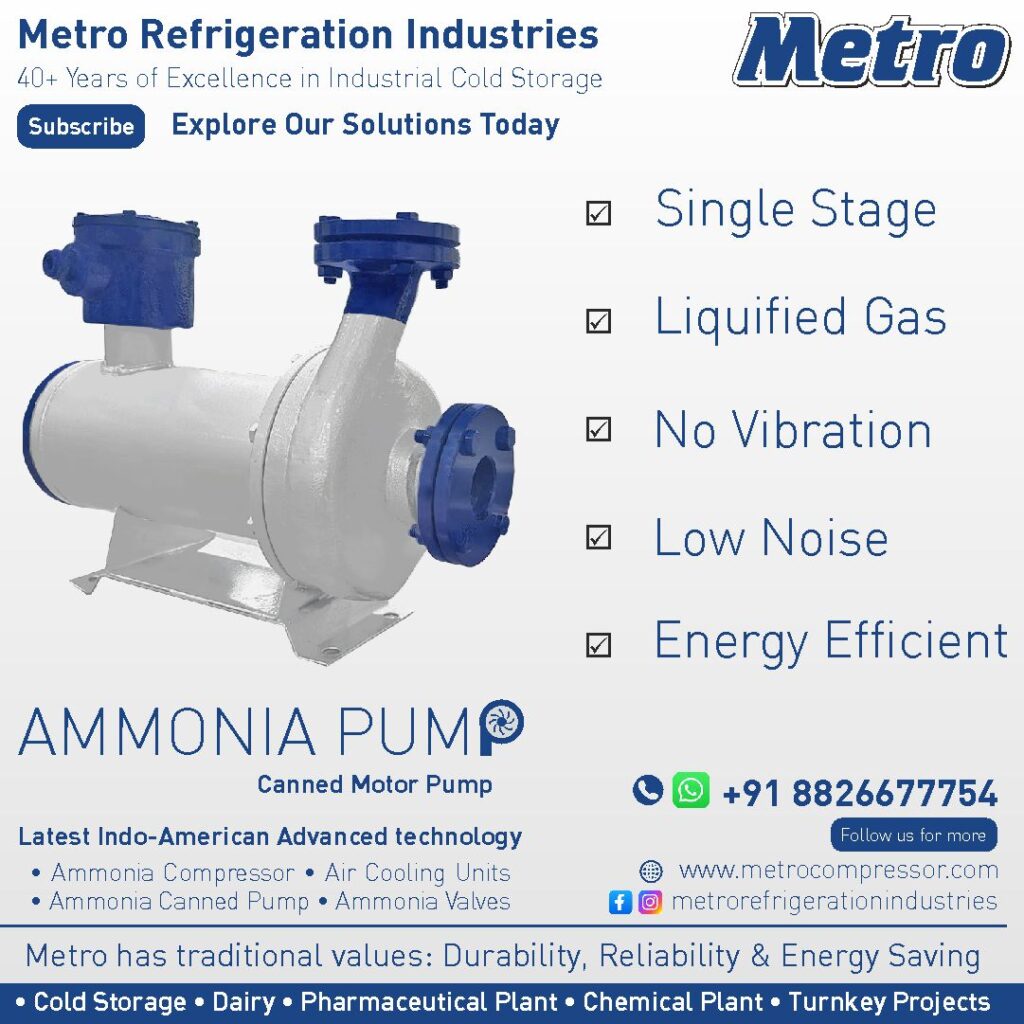
-
Ammonia Pumps and Valves
- Purpose: Facilitates the safe and efficient circulation of ammonia refrigerants in large cooling systems.
- Applications: Critical for industrial-scale meat processing plant refrigeration setups.
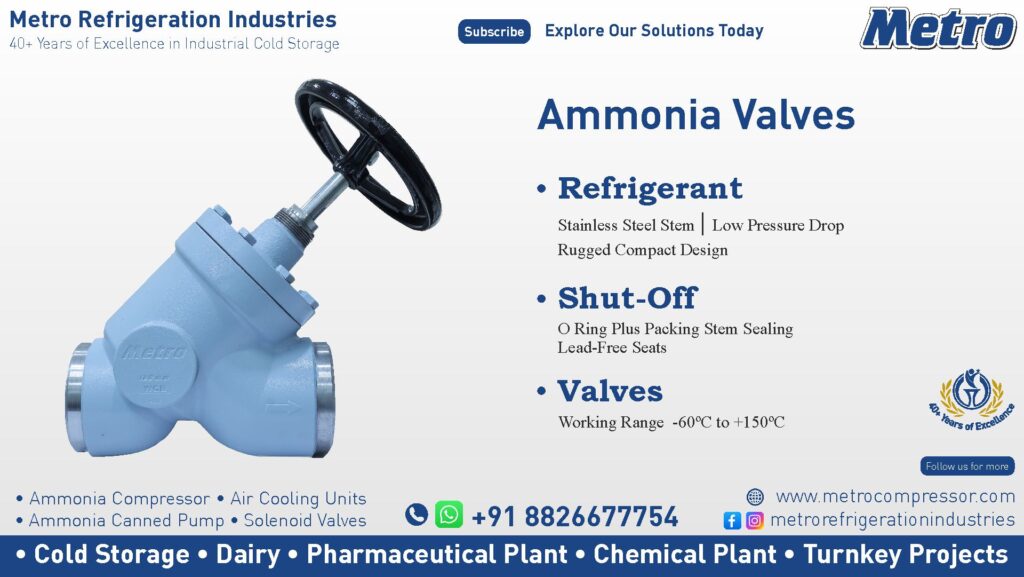
-
Air Cooling Units
- Purpose: Ensures uniform cooling by circulating chilled air in cold storage or processing areas.
- Applications: Maintains temperature stability in meat processing plant layouts.
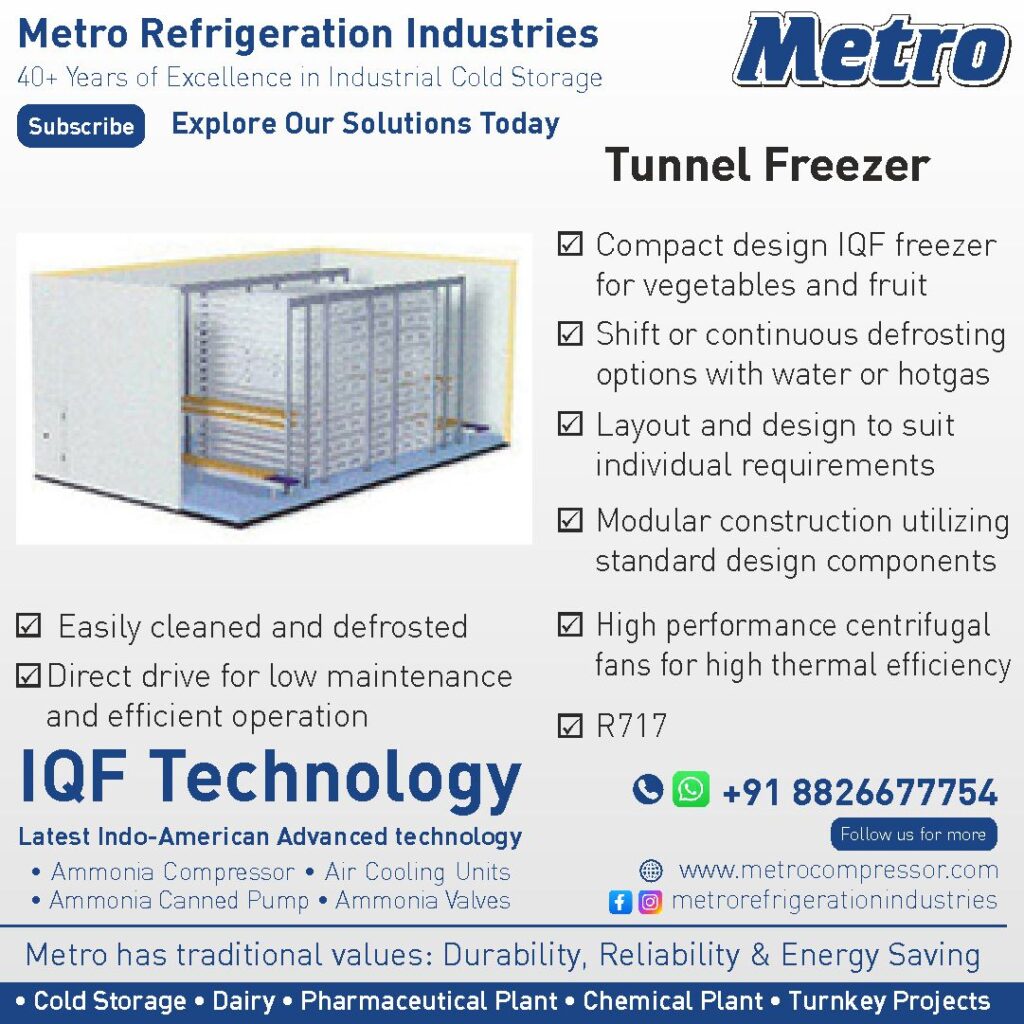
-
Blast Freezers
- Purpose: Quickly freezes meat products to maintain their natural texture, flavor, and quality.
- Applications: Used for bulk freezing of processed meat like beef, chicken, and lamb.
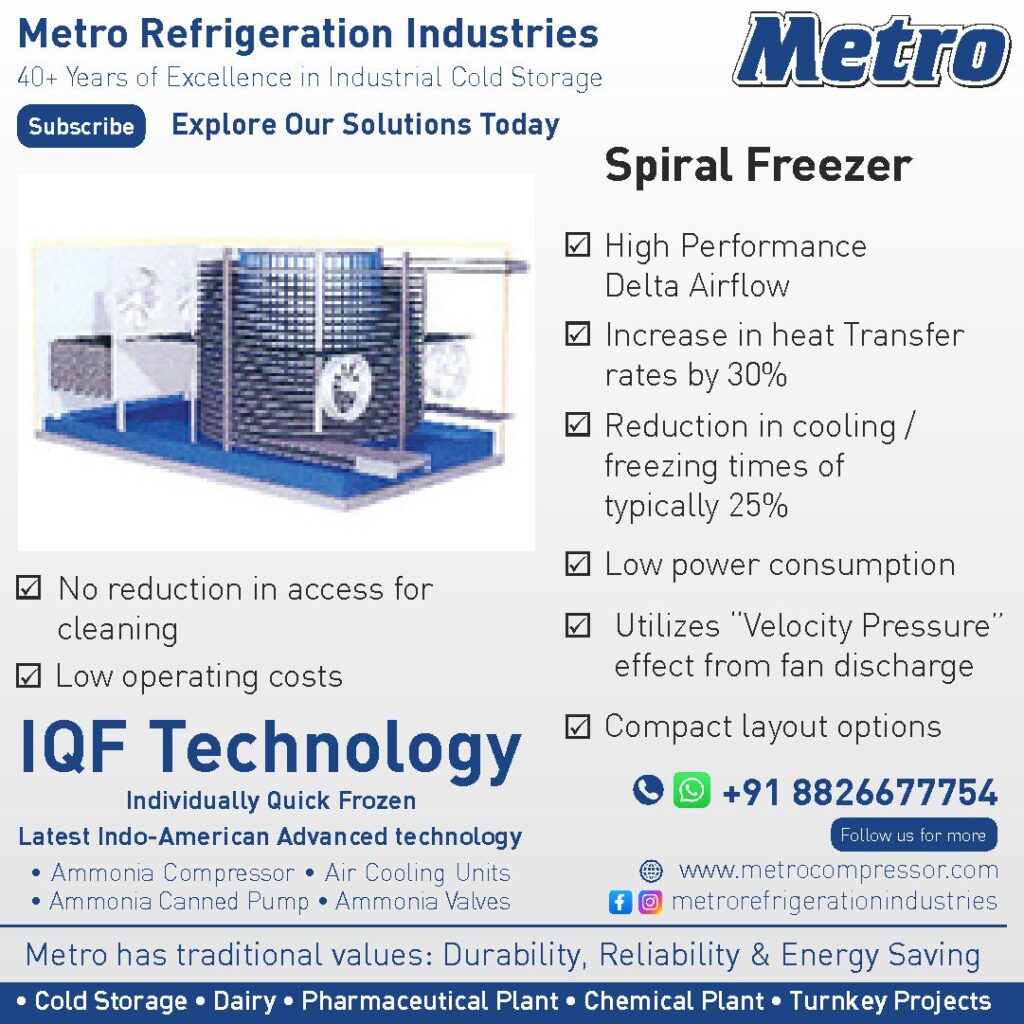
-
Blast Chillers
- Purpose: Rapidly reduces the temperature of freshly processed meat to inhibit bacterial growth and preserve freshness.
- Applications: Ideal for chilling meat carcasses, poultry, and seafood immediately after processing.

-
Individual Quick Freezing (IQF) Systems
- Purpose: Freezes individual pieces of meat or seafood, preventing clumping and ensuring easy handling.
- Applications: Commonly used for chicken wings, seafood, and small meat cuts.
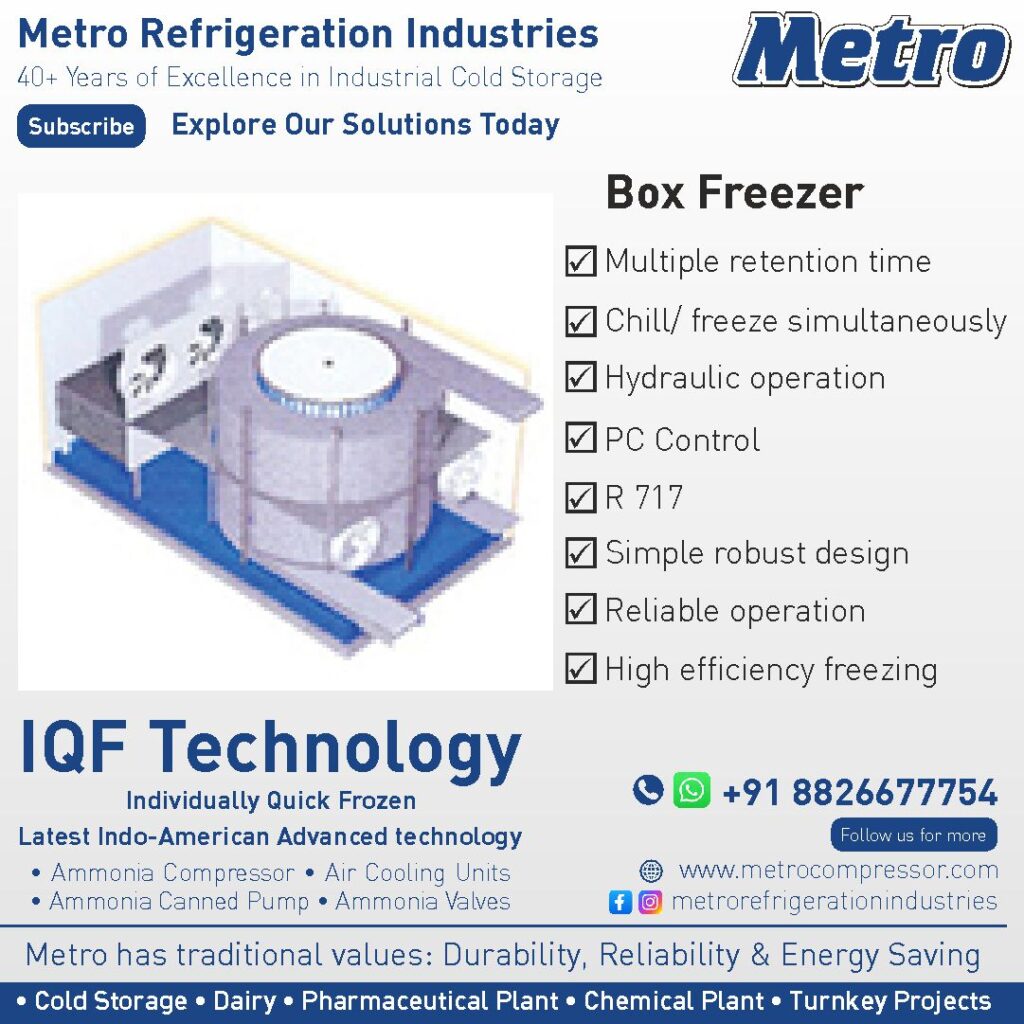
-
Cryogenic Freezers
- Purpose: Achieves ultra-low temperatures for flash freezing using liquid nitrogen or carbon dioxide.
- Applications: Suitable for high-value meat cuts and seafood like crabs or shrimp.
-
Super Freezers
- Purpose: Freezes meat at extremely low temperatures for specialized applications.
- Applications: Used for high-value products requiring long-term preservation.
-
Rapid Freezing Units
- Purpose: Quickly freezes freshly processed meat for maximum freshness and safety.
- Applications: Common in poultry, seafood, and specialty meat processing facilities.
-
Meat Plant Refrigeration Controllers
- Purpose: Monitors and adjusts temperature, humidity, and other refrigeration parameters.
- Applications: Ensures precision in maintaining optimal conditions for different meat types.
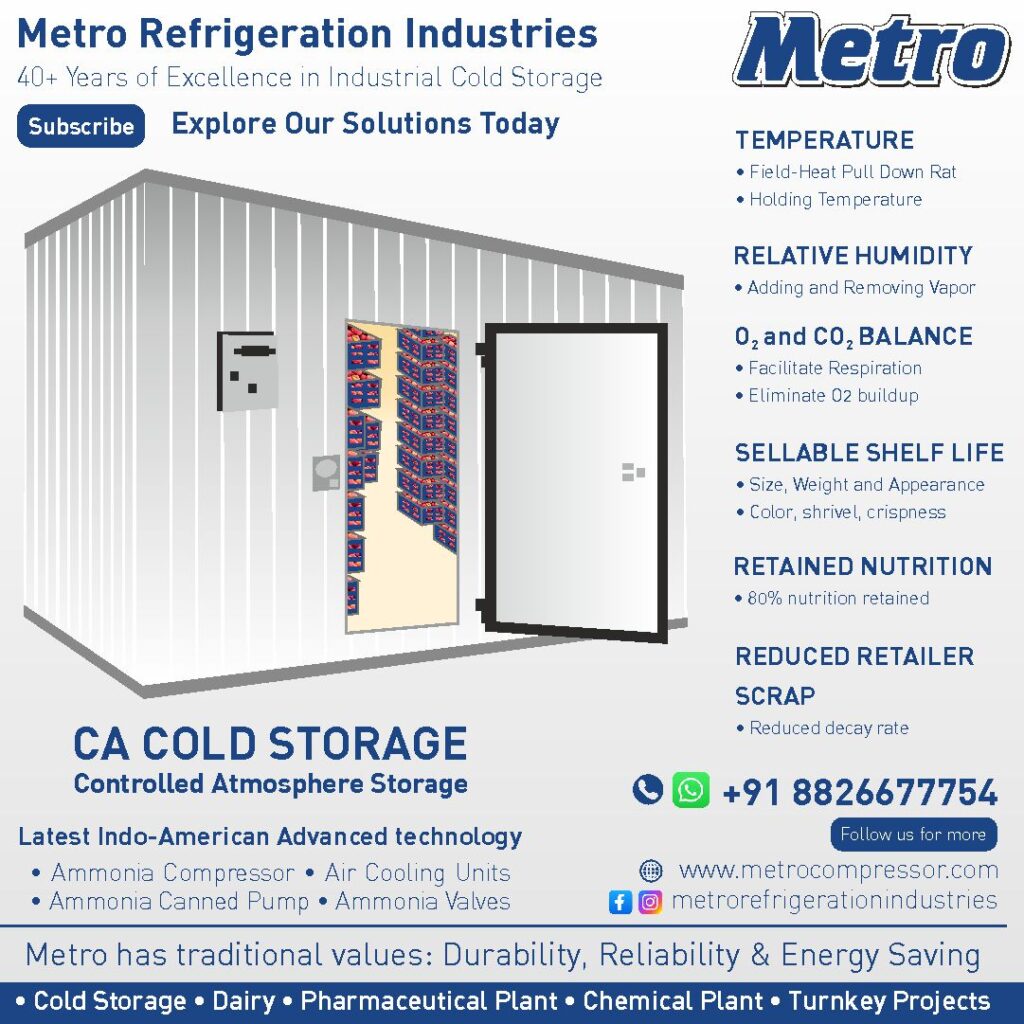
-
Cold Rooms
- Purpose: Provides long-term refrigerated storage for frozen meat products.
- Applications: Used for storing frozen chicken, processed meat, and other frozen goods.
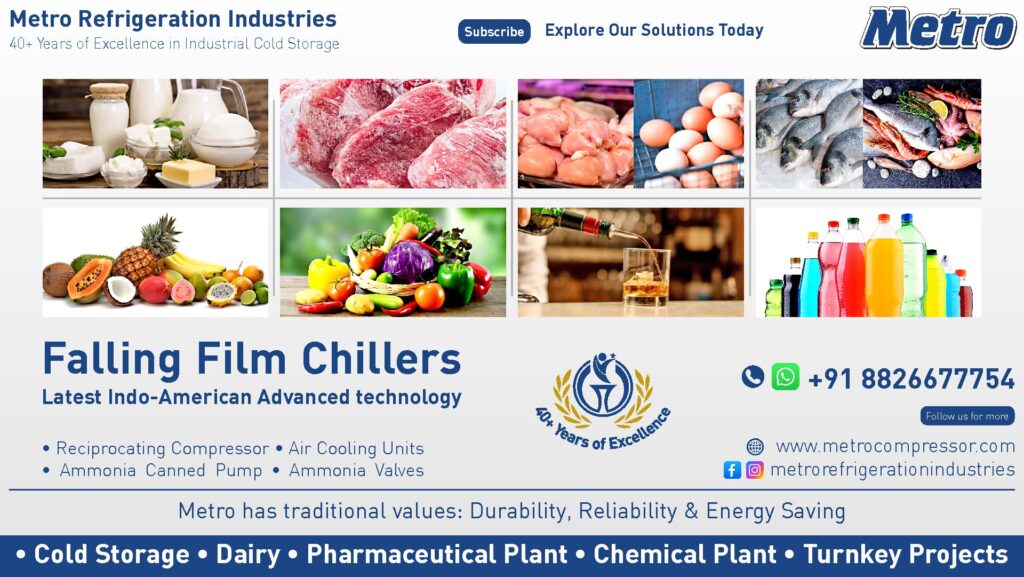
-
Chiller Rooms
- Purpose: Maintains a controlled temperature for short-term storage of meat prior to further processing or packaging.
- Applications: Suitable for storing poultry, beef, and pork in pre-processing stages.
At Metro Refrigeration Industries, we specialize in providing ammonia-based refrigeration solutions designed for meat processing facilities. Our systems are efficient, energy-saving, and incorporate advanced Indo-American technology to ensure optimal conditions for meat preservation.
Installation and Setup
Work with experienced professionals for the installation and commissioning of your chilling plant unit. Metro Refrigeration Industries provides complete turnkey solutions, including:
- Design and construction support
- Energy-efficient machinery installation
- Maintenance and after sales support
- Manufacture and commissioning of complete industrial ammonia refrigeration system, equipment, and machineries.
Modern meat processing plants, whether for beef, pork, poultry, or seafood, are essential for a thriving meat industry. With innovations like IQF technology, super freezing, and CA cold storage, these facilities offer unmatched quality and efficiency.
Partner with Metro Refrigeration Industries to build your state-of-the-art facility today!
Complete Product Line
Our advanced product line includes:
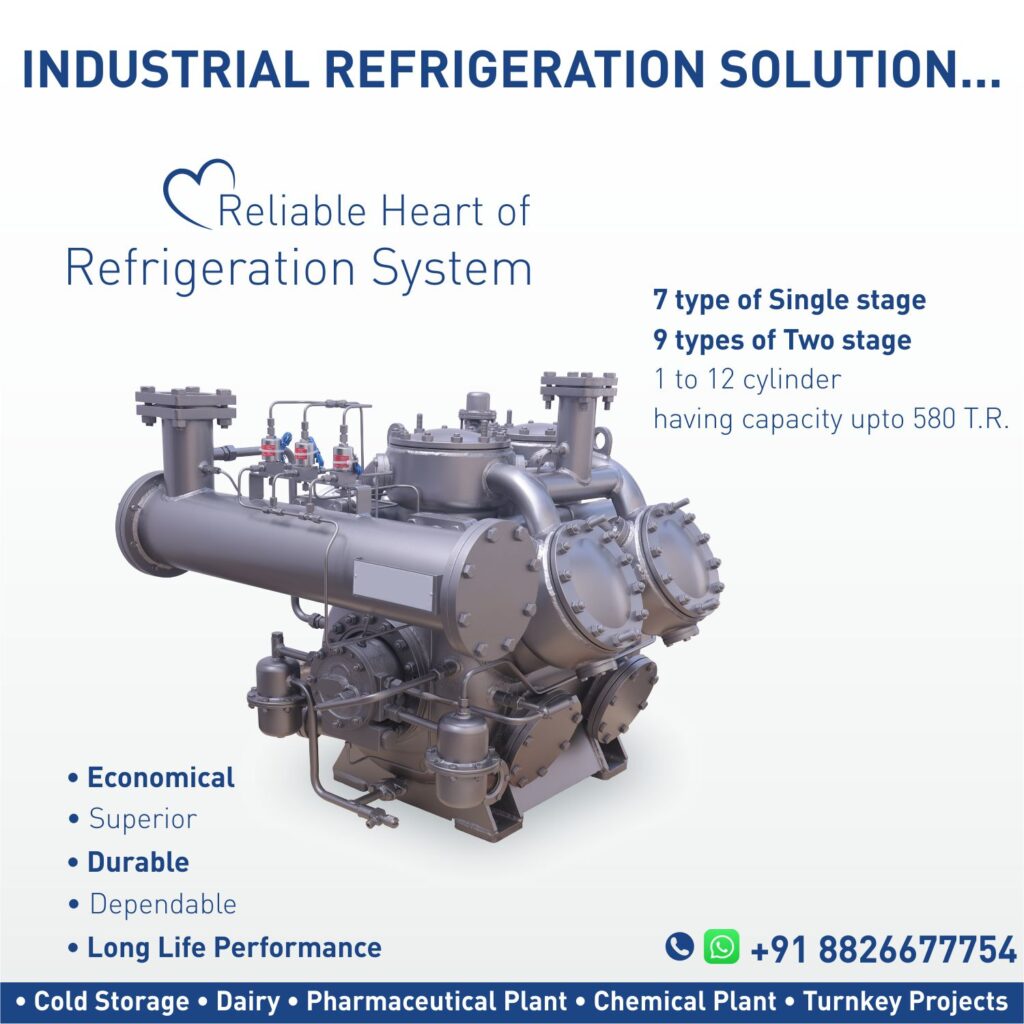
Ammonia Compressor: Backbone of Industrial Ammonia Refrigeration System
Our Nh3 refrigeration compressor are designed to deliver unmatched performance, ensuring reliability and efficiency across a wide range of applications. The range includes:
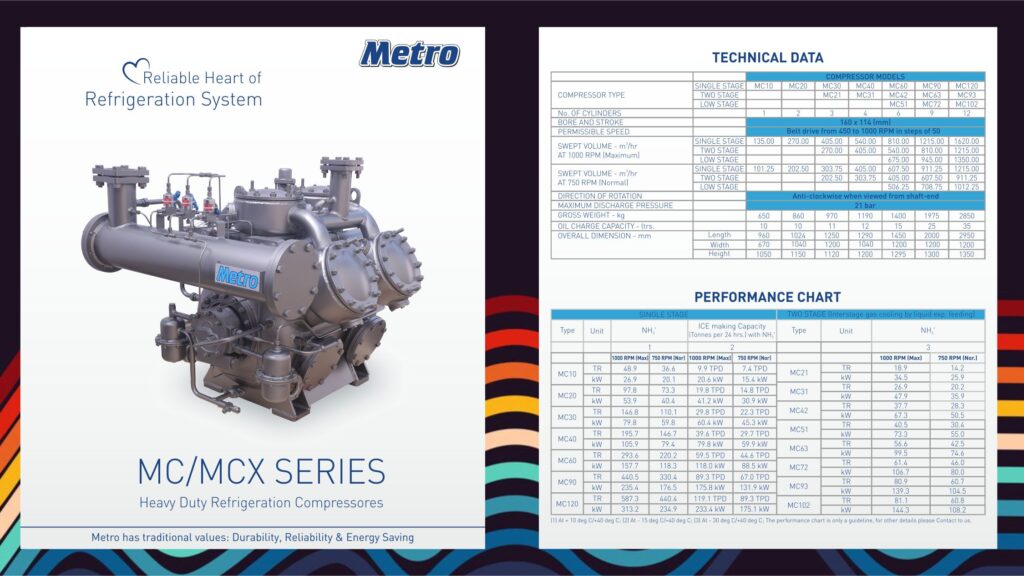
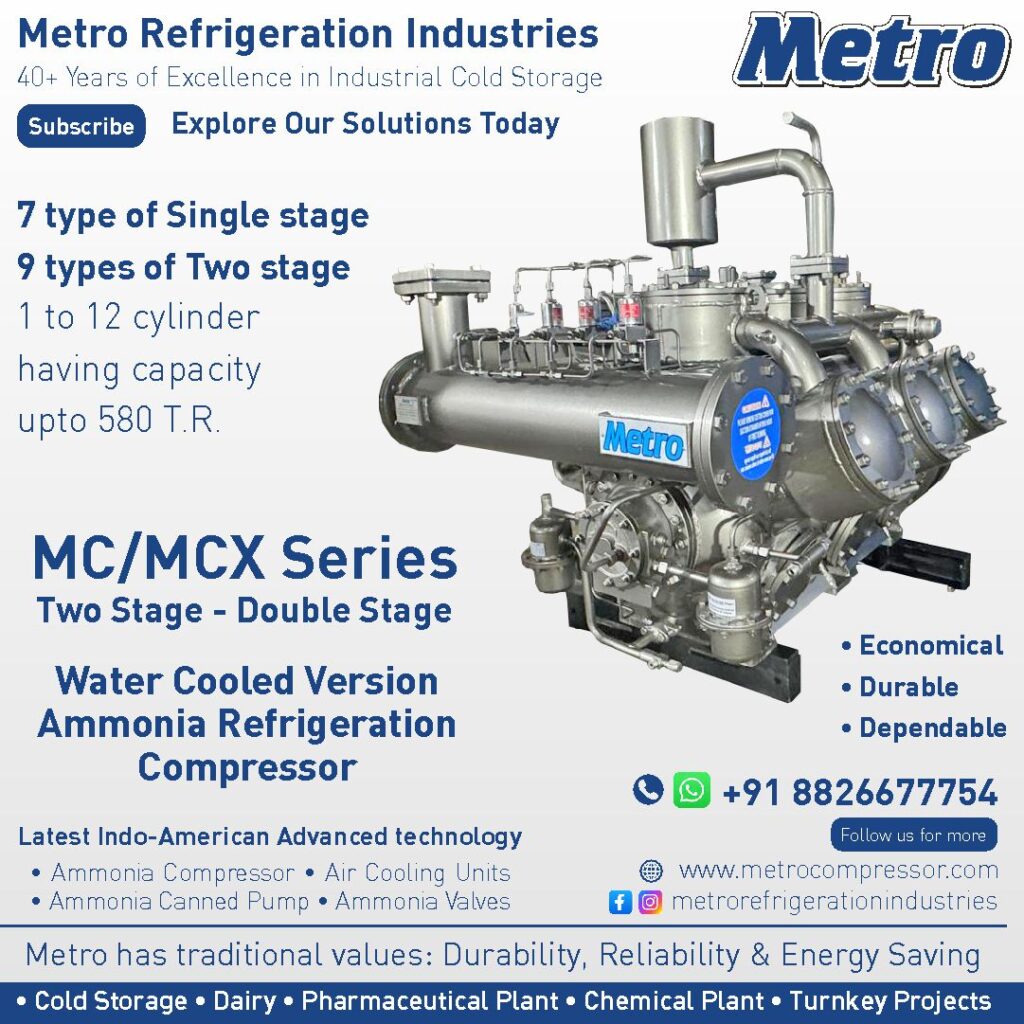
- MC Series (Water Cooled Nh3 Compressor): Ideal for industries requiring consistent cooling under extreme conditions.
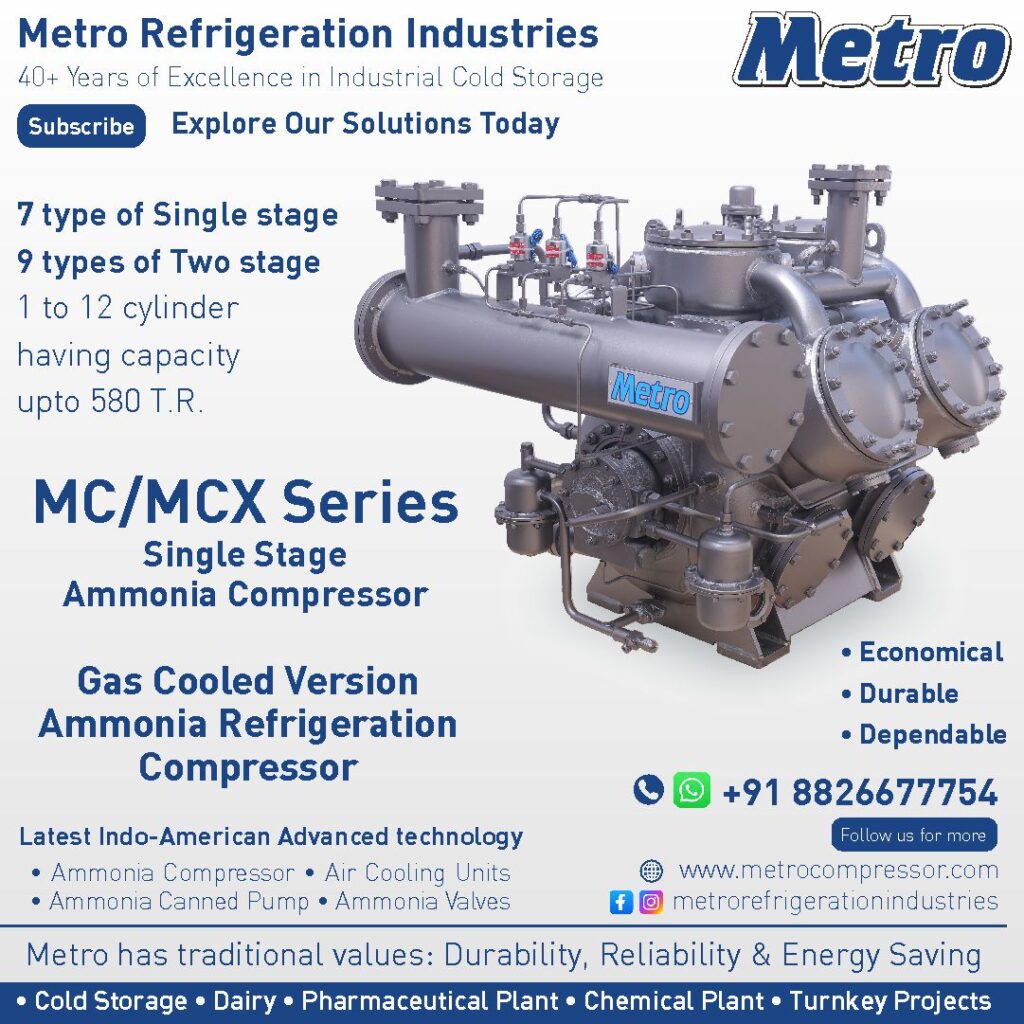
- MCX Series (Gas Cooled Nh3 Compressor): Designed for energy-efficient operation in diverse environments.
Comprehensive Range of Nh3 Compressor
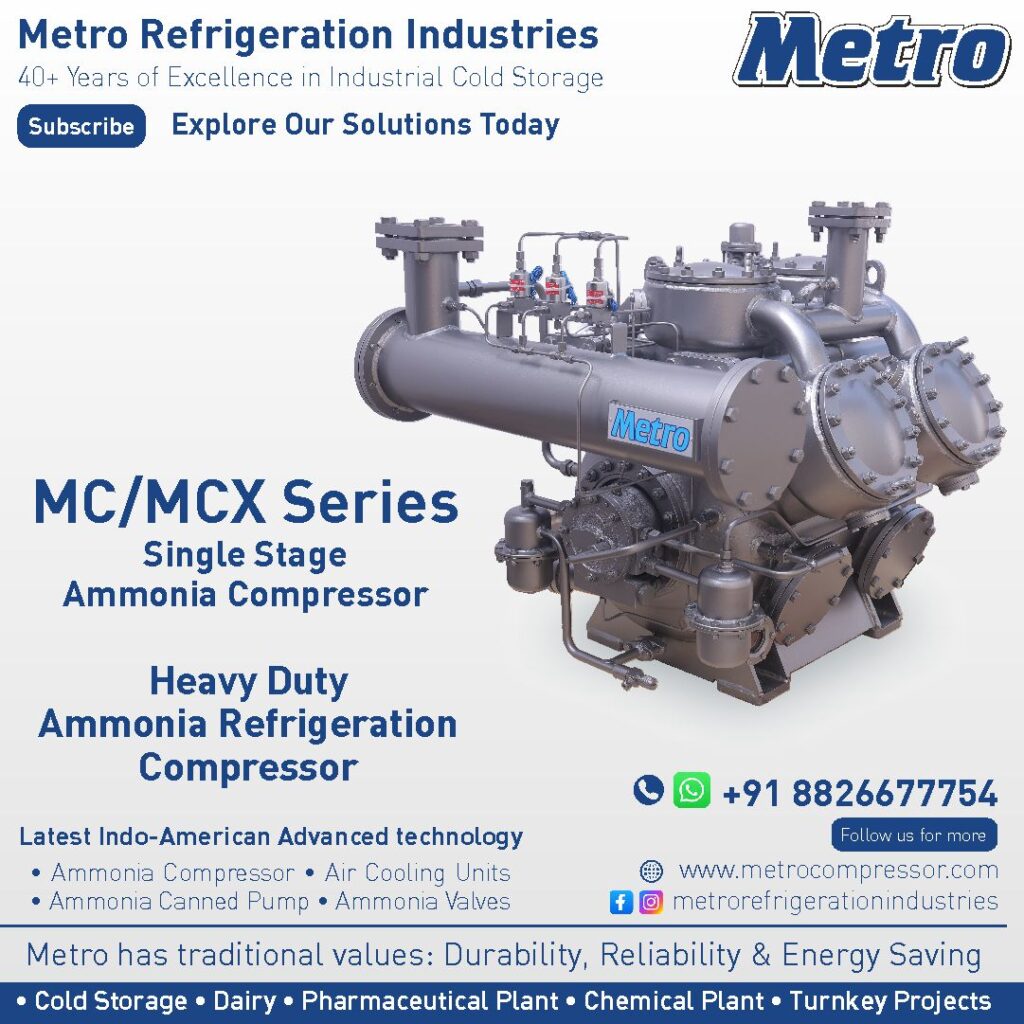
- Single Stage Ammonia Compressor: Available in 7 types, featuring 1 to 12 cylinders with capacities up to 580 T.R. These refrigeration compressor are perfect for moderate refrigeration requirements.
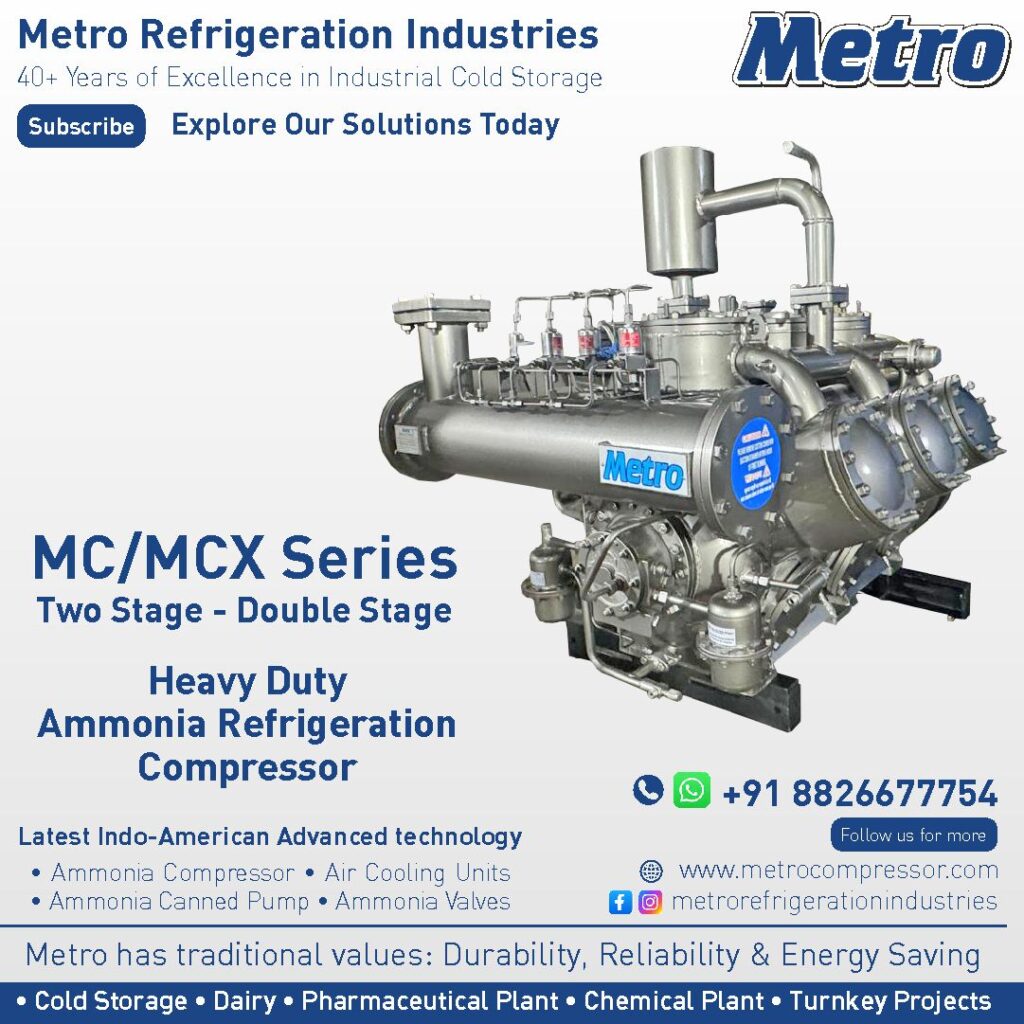
- Two Stage Ammonia Compressor (Compound Version): Available in 9 types, featuring 1 to 12 cylinders with capacities up to 580 T.R. Engineered for applications requiring precise temperature control at low and ultra-low temperatures.
Additional Equipment and Solutions
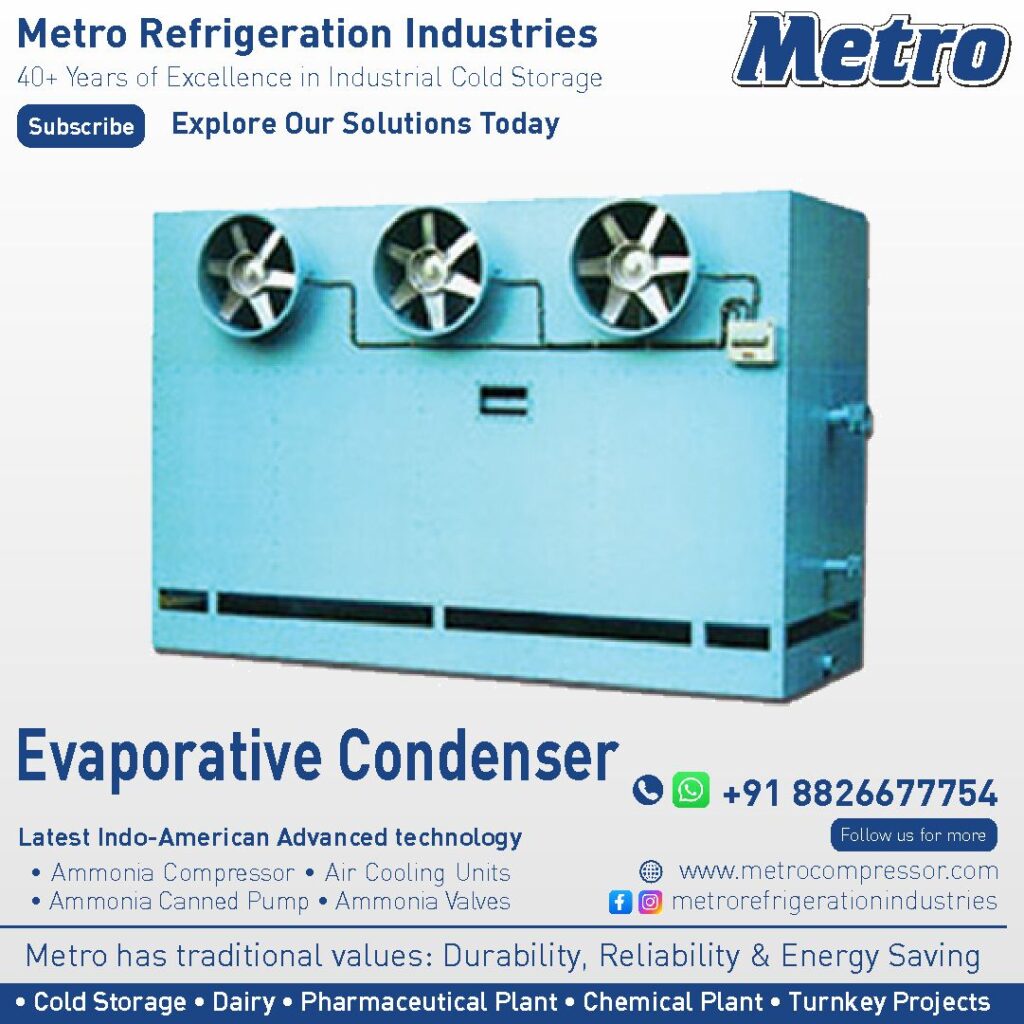
- Evaporative Condenser: Engineered for maximum heat transfer and reduced energy consumption in refrigeration systems.
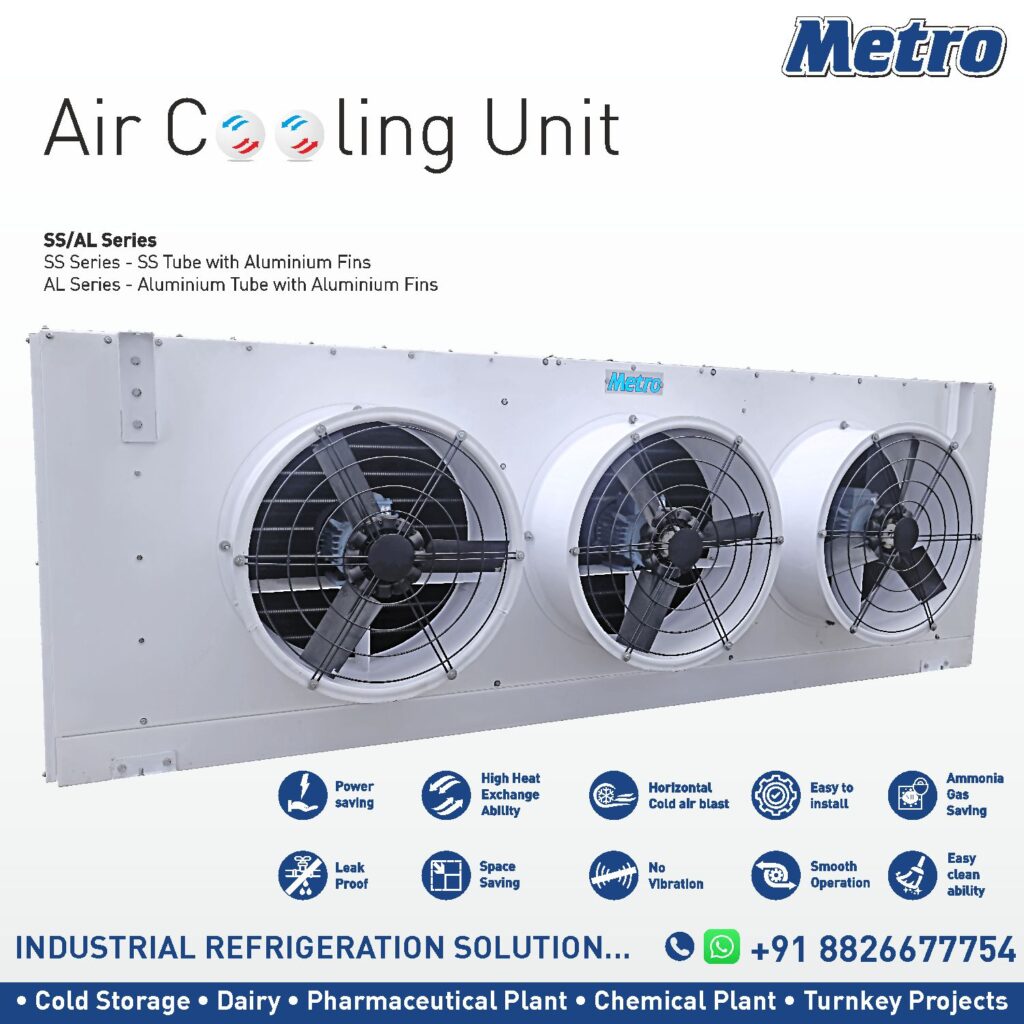
- Air Cooling Units: SS and AL Series durable and efficient cooling solutions, including stainless steel and aluminum options.
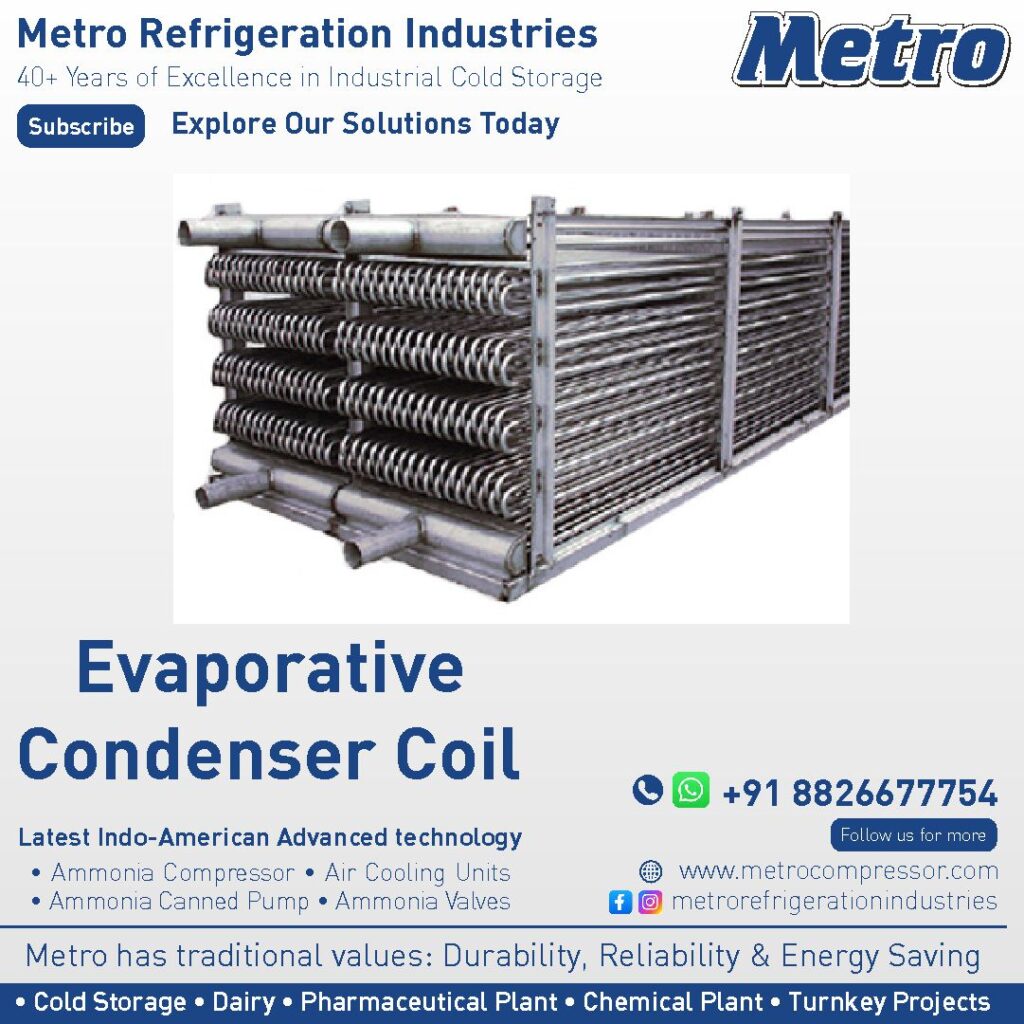
- Evaporator Coils: Ensure consistent cooling performance with our advanced ammonia evaporator coils.
- Ammonia Evaporative Coolers: Energy-saving Nh3 cooling systems for industrial applications.
- Cooling Coil Units: Maintain temperature precision with our high-performance cooling coil units.
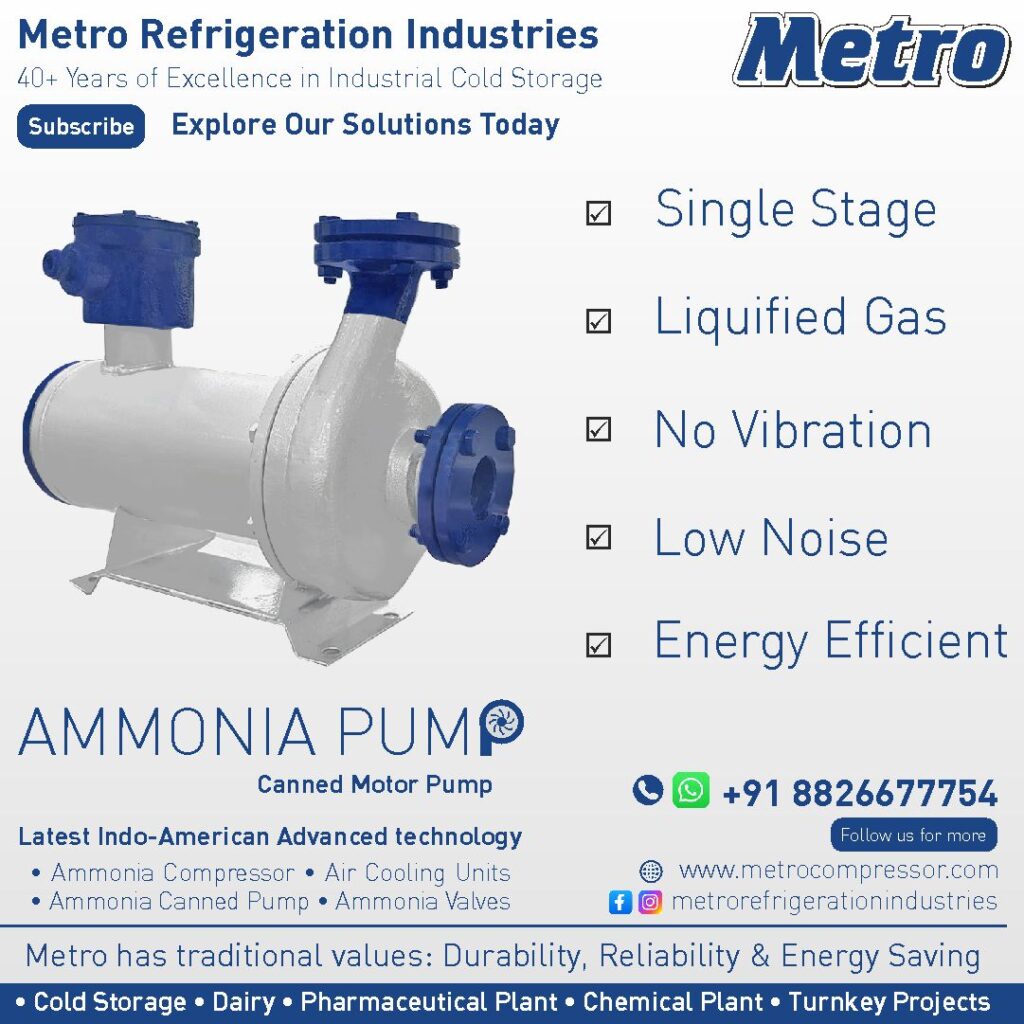
- Ammonia Canned Pumps: Built for reliable ammonia transfer in industrial refrigeration systems.
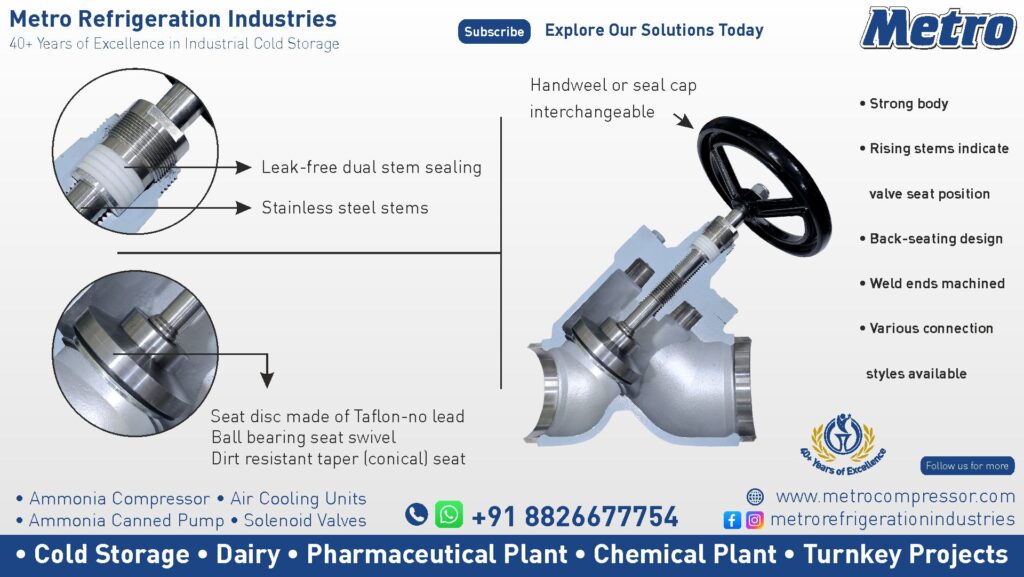
- Ammonia Valves: Precision-engineered valves for safe and efficient ammonia flow control.
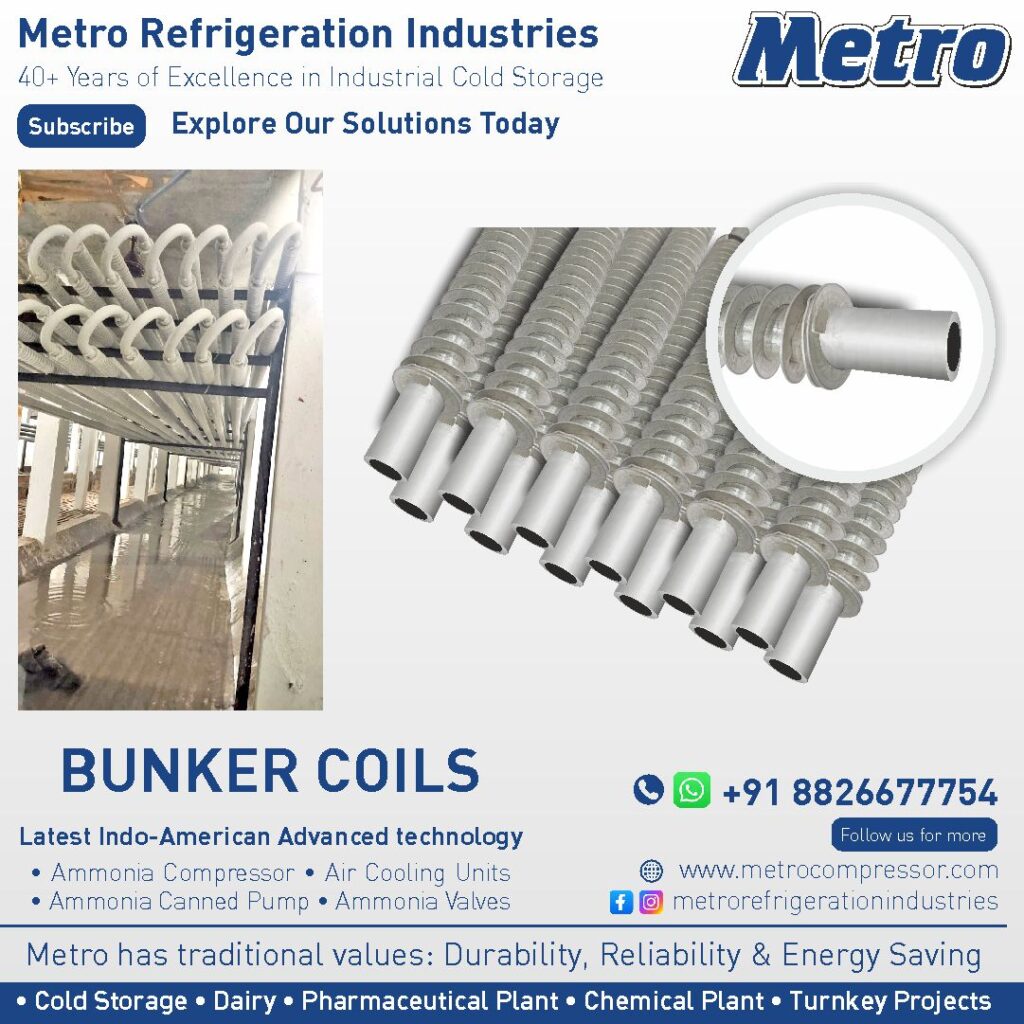
- Bunker Coils: High-efficiency heat transfer coils for industrial refrigeration processes.
- LPR & HPR: Optimize refrigeration system performance with low pressure receivers and high pressure receivers.
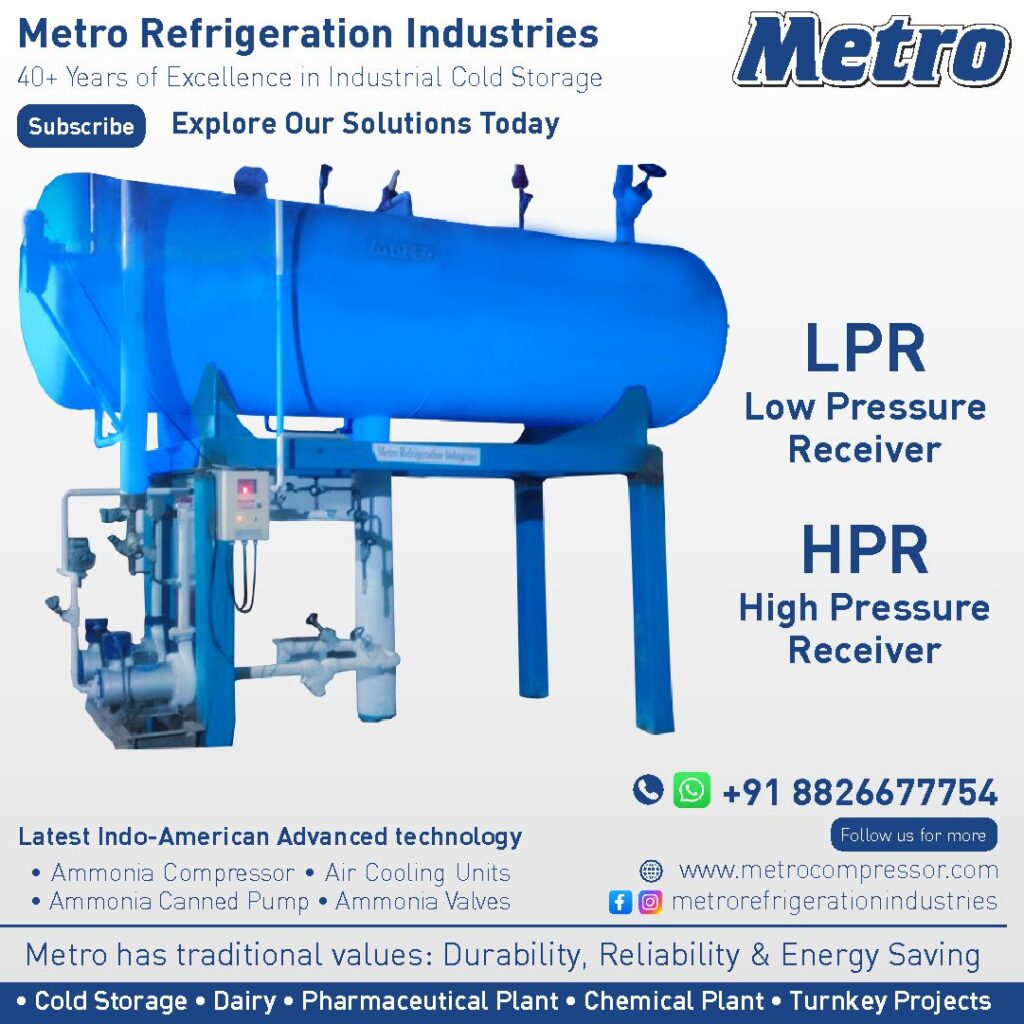
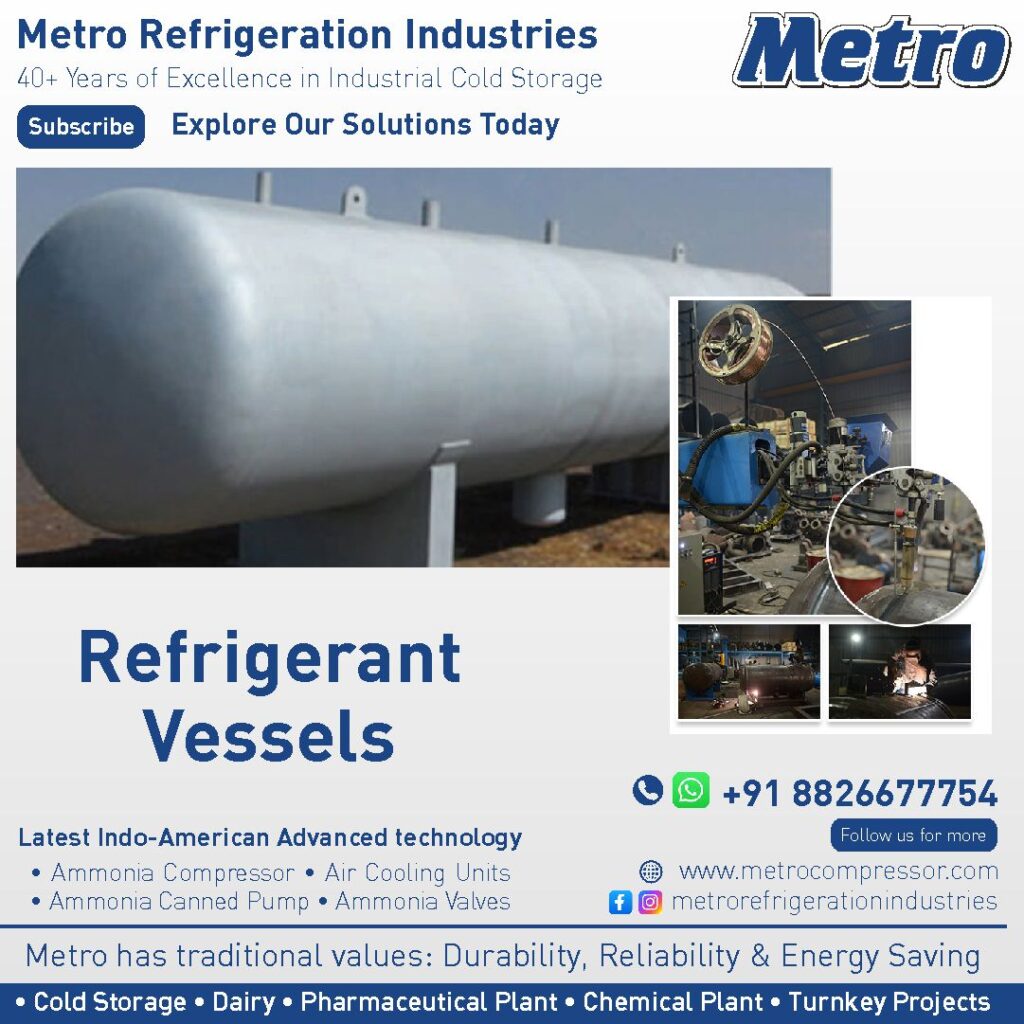
- Refrigerant Vessels: Secure and efficient refrigerant storage solutions for industrial use.
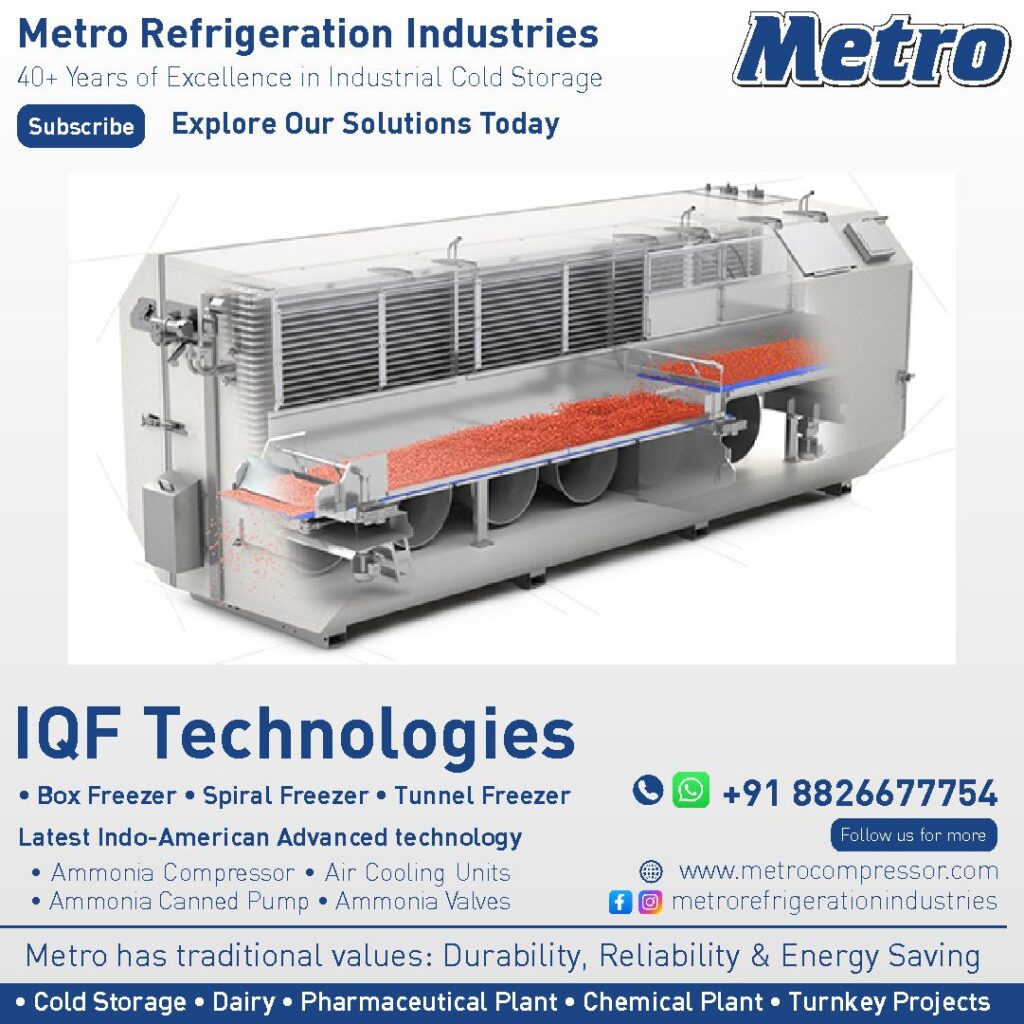
- IQF Technology: Advanced freezing technology to preserve food quality and extend shelf life.
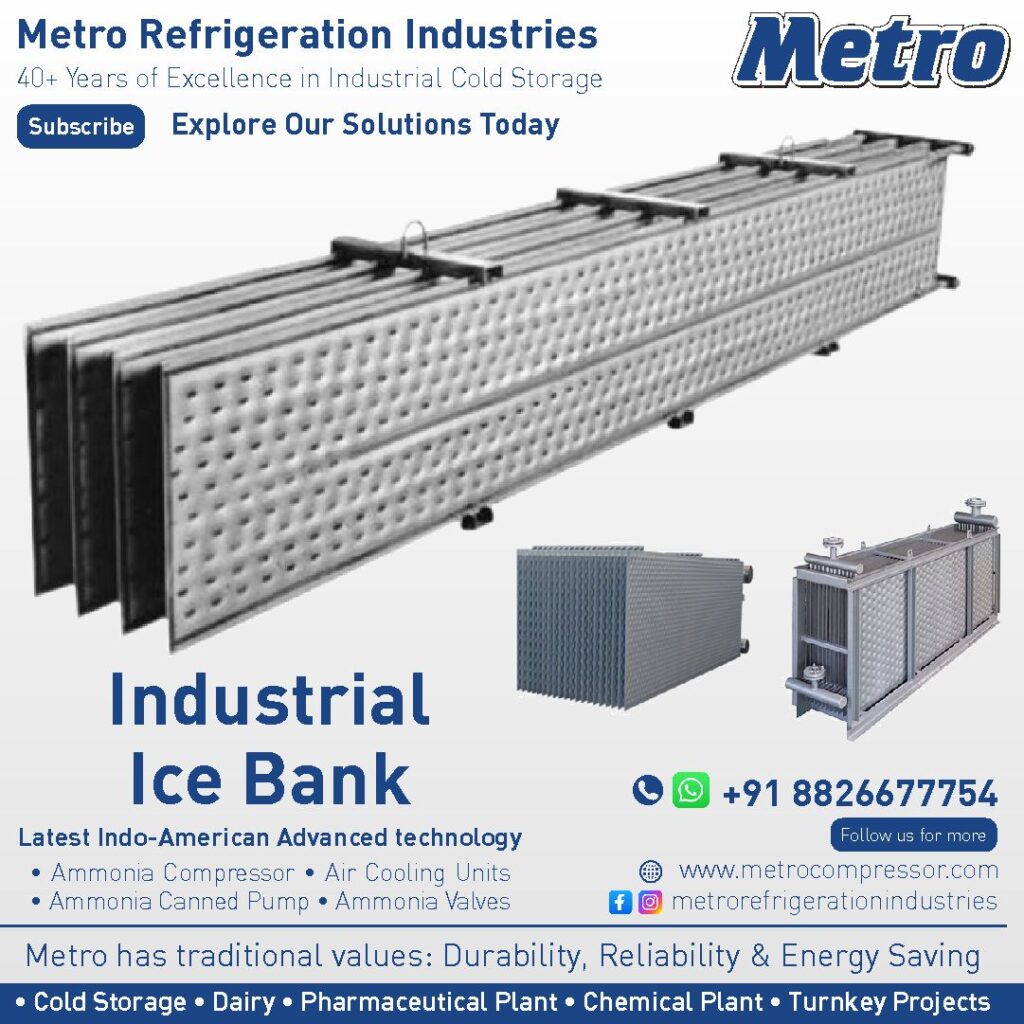
- Industrial Ice Bank: Dependable ice storage systems for industrial cooling needs.
- Pillow Plates: Effective heat exchange solutions for refrigeration and industrial applications.
- Axial Fans: Improve airflow and cooling performance with durable axial fans.
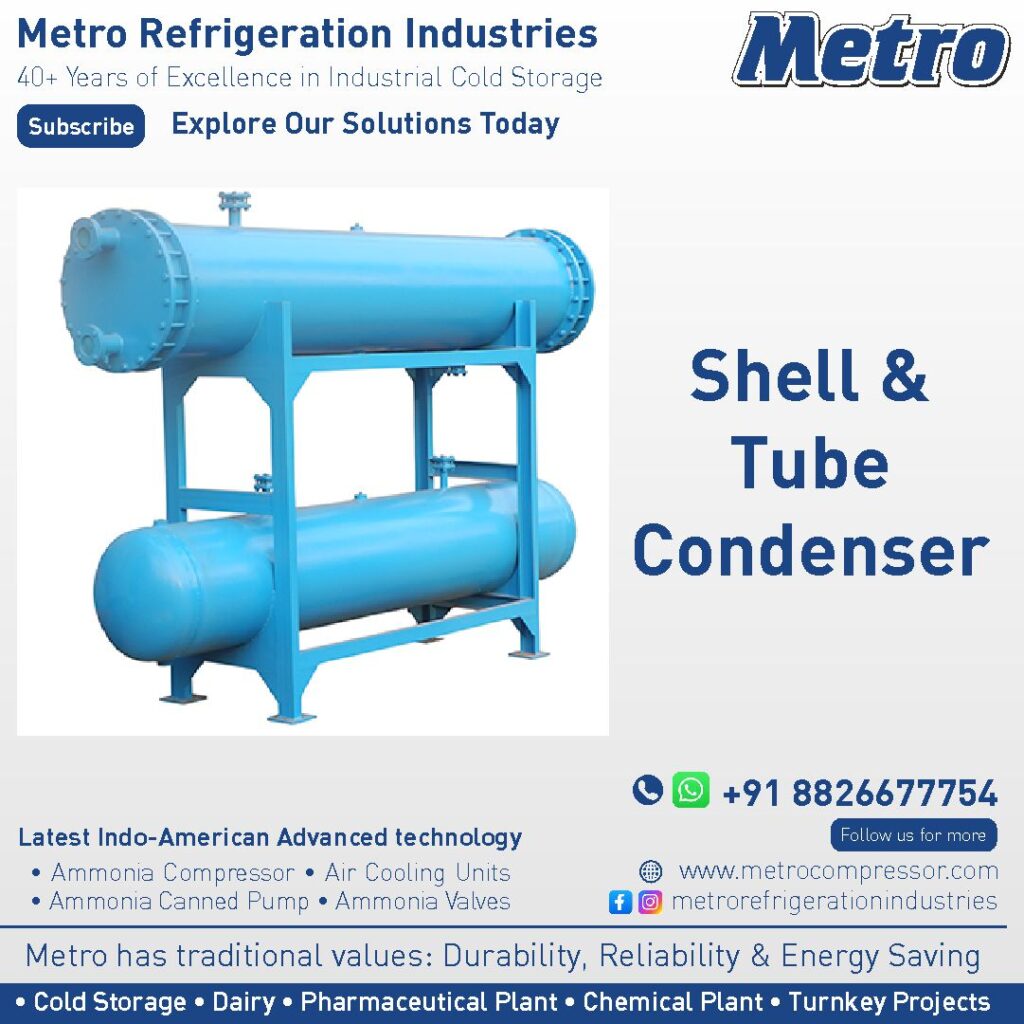
- Shell & Tube Condensers: Robust condensers designed for high-capacity industrial refrigeration.
- Ammonia Compressor Components: Ensure optimal operation with precision-engineered ammonia refrigeration compressor components.
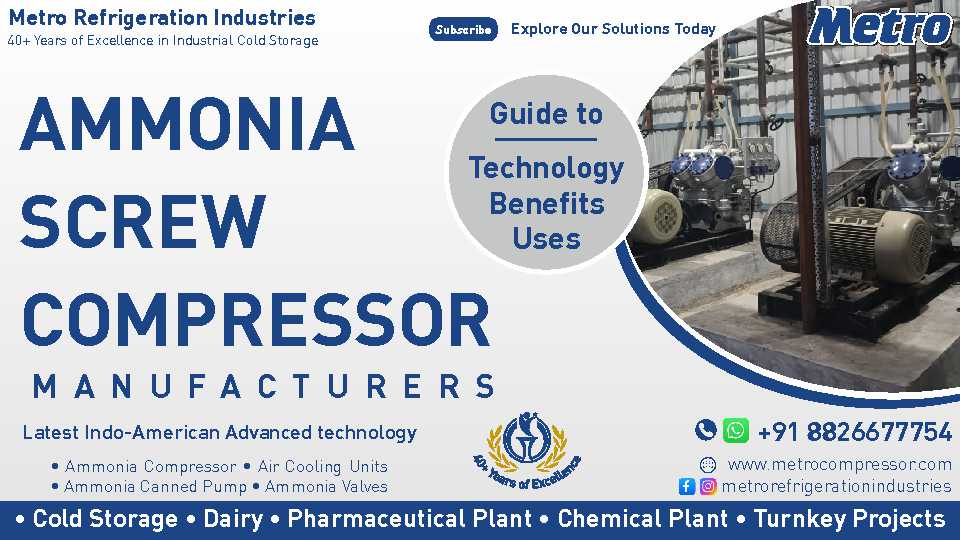
- Brine Chillers: Discover high performance ammonia brine refrigeration systems from leading brine chiller manufacturers. Our brine chiller plants, brine cooling systems, and brine refrigeration solutions ensure energy efficient industrial cooling. We also specialize in ammonia screw compressors and shell & tube condensers, delivering cost effective and reliable cooling solutions for various industries.
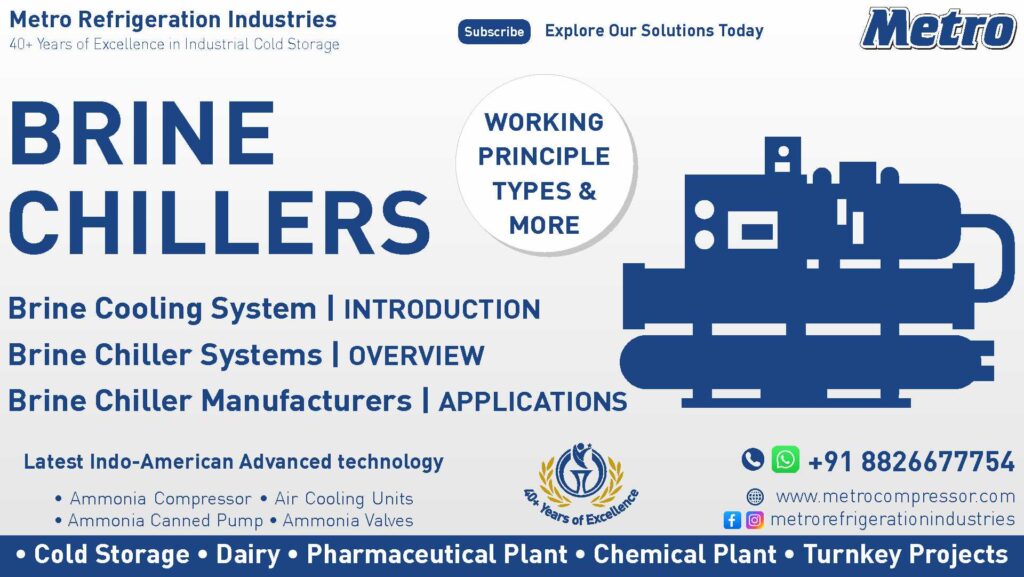
-
- Ammonia Compressor Components: Ensure optimal operation with precision-engineered ammonia refrigeration compressor components.
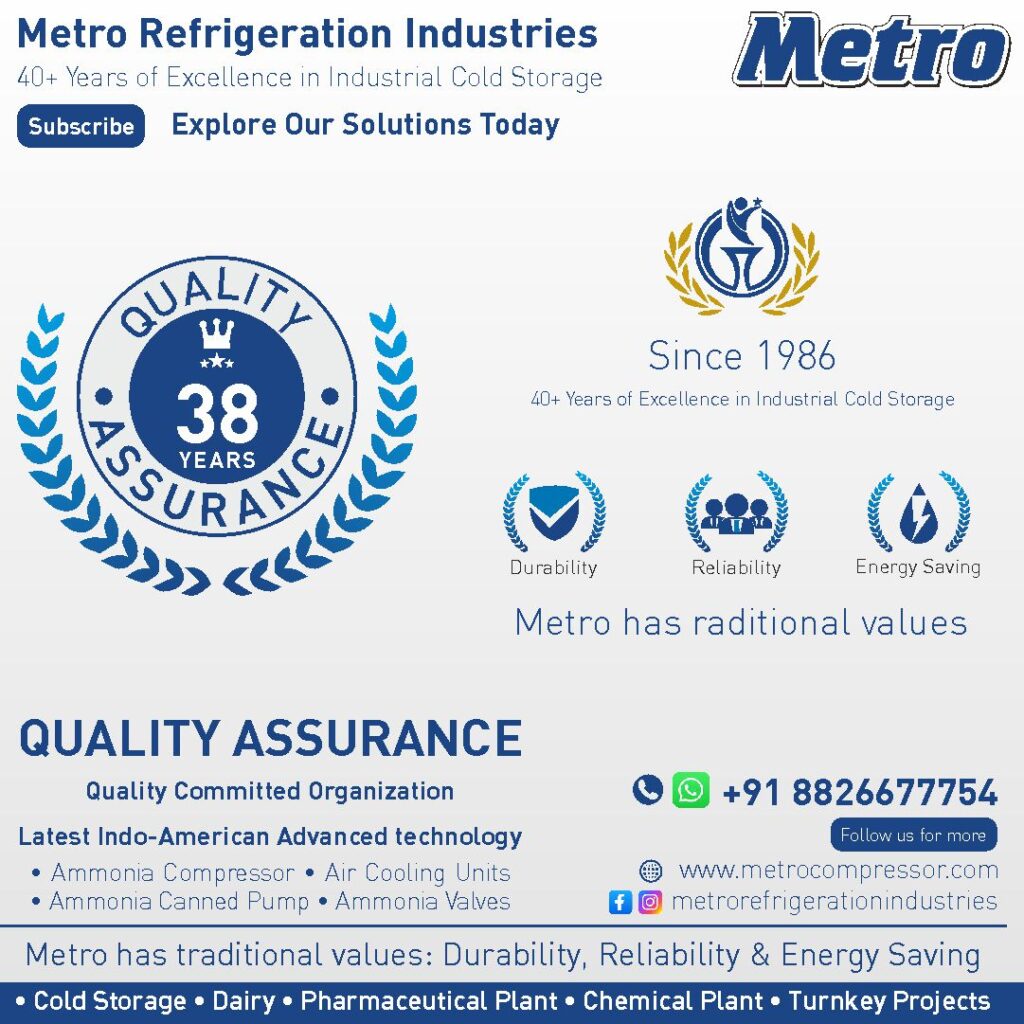
Why Choose Metro Refrigeration Industries?
Experience: Over 40 years of expertise in designing and manufacturing meat processing unit solutions.
Global Presence: Serving clients in India and over 30 countries worldwide, including Australia, UAE, Jordan, Turkey, Yemen, Thailand, Sri Lanka, and Nepal.
Cutting-Edge Indo-American Technology: Ensures superior energy efficiency and performance.
Prestigious Clientele: Trusted by Amul, Adani, Namaste India, Patanjali, and more.
Complete Product Line: Comprehensive range of equipment tailored for cold storage, including ammonia compressors, ammonia evaporators, evaporative condensers, air cooling units, evaporator coils, ammonia valves, and more.
Best Cold Storage System Equipment and Machineries: Designed for reliability, energy efficiency, and precise temperature control.
Cost-Effective Solutions: Delivering low energy consumption and precise temperature control.
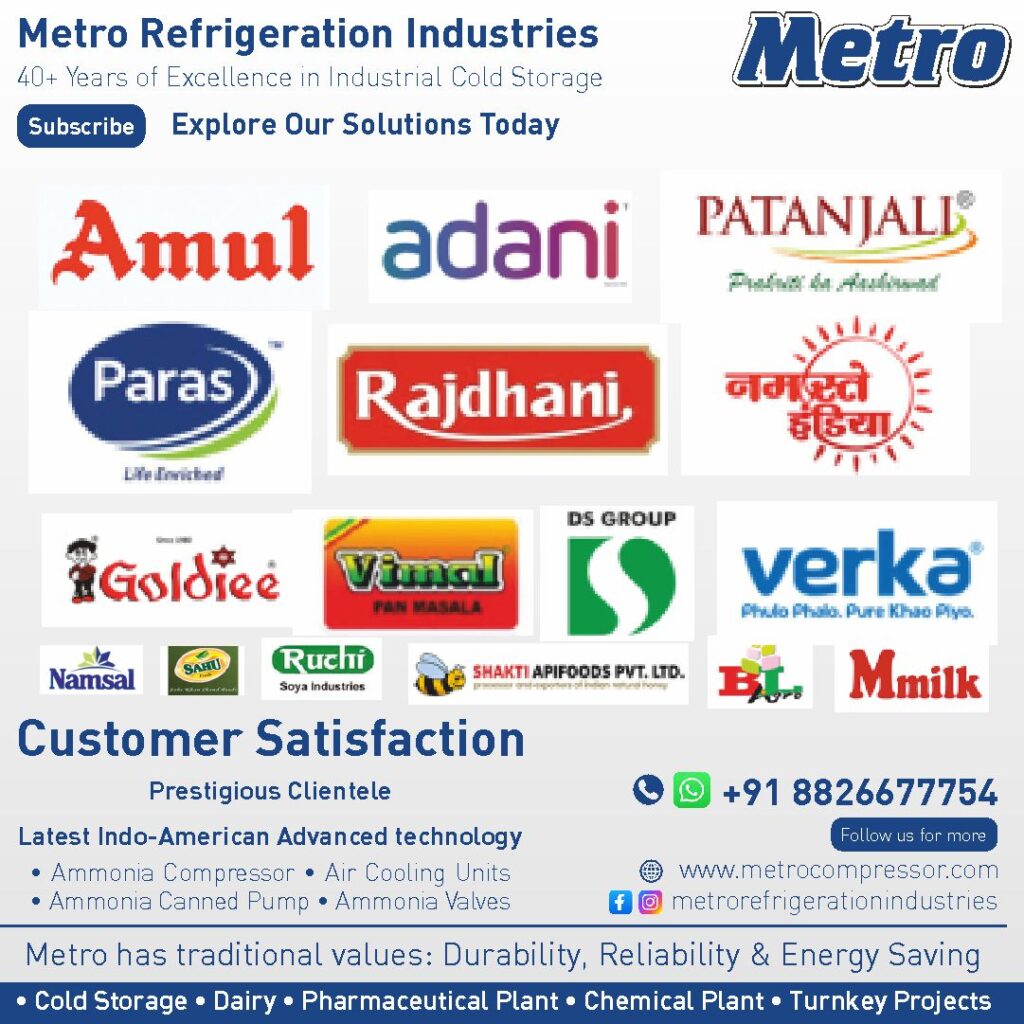
Optimizing Your Cold Storage with Metro Refrigeration
At Metro Refrigeration Industries, we understand the importance of having a reliable and efficient cold storage system. We offer custom cold storage design and can guide you through the cold storage operation to ensure optimal performance. Our engineers are skilled in the optimization of your cold storage system, ensuring it operates at peak efficiency.
Our cold storage plant designs incorporate advanced technology that helps in refrigerated unit optimization, resulting in lower operational costs and improved product quality.
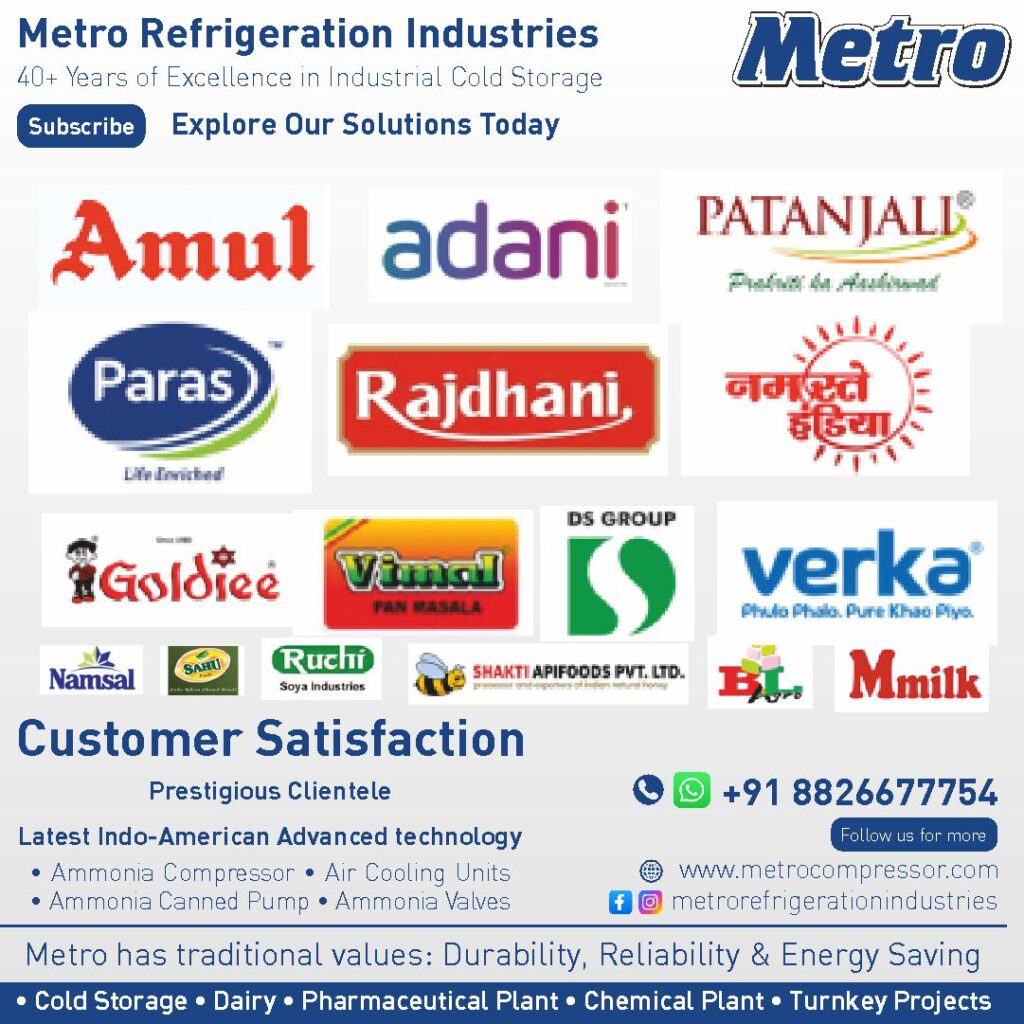
Partner with Metro Refrigeration Industries for Turnkey Cold Storage Solutions
Metro Refrigeration Industries offers industry-leading expertise and technology for all your industrial ammonia refrigeration needs. Whether it’s agriculture, dairy, or industrial refrigeration, we deliver customized, energy-efficient, and cost-effective solutions. Contact us today to explore how our expertise can support your business growth.
Get in touch with us for cost-effective and reliable refrigeration solutions and join the leading names in the industry who trust Metro Refrigeration Industries.
Conclusion
Refrigeration unit is an indispensable component of modern industries, ensuring the preservation of perishable goods and the seamless functioning of supply chains. Whether it’s agricultural produce, dairy, meat, pharmaceuticals, or industrial applications, cold storage facilities cater to a wide range of needs, supporting economic growth and sustainability.
With advancements in refrigeration technologies like ammonia and freon systems, and the introduction of controlled atmosphere (CA) storage, businesses can now achieve higher efficiency and cost-effectiveness. Companies like Metro Refrigeration Industries lead the way with innovative solutions, a complete product line, and a robust global presence, serving the needs of diverse industries across India and 30 international markets.
Investing in refrigerated plant not only reduces wastage and ensures quality but also drives economic benefits for farmers, businesses, and the nation. With proper planning, subsidies, and partnerships with top cold storage manufacturers, setting up a plant facility is a promising venture for long-term success.
If you’re looking for reliable, energy-efficient, and advanced cold storage solutions, Metro Refrigeration Industries is your trusted partner. With decades of expertise, cutting-edge technology, and a commitment to quality, we bring you the best in refrigeration. Contact us today to explore cost-effective and customized solutions tailored to your needs.
Contact Metro Refrigeration Industries
To explore our products and solutions for your refrigeration unit, get in touch:
Location: D-35, Meerut Road Industrial Area, Ghaziabad, Uttar Pradesh – 201 003, INDIA
Email: sales@metrorpl.com
Phone: +91-120-2712176, 2752030, 2757568, 2757269, 2713759
Customer Care: +91 88266 77754
Website: www.metrocompressor.com
Explore more related blogs:
Meat Processing Plant
We specialize in manufacturing cutting-edge refrigeration solutions for meat processing, catering to beef, chicken, cattle, seafood, fish, prawns, crabs, and frozen chicken. Our advanced systems ensure precise temperature control, freshness, and quality preservation. Trusted by industries for energy efficiency and durability, we provide comprehensive solutions tailored to meet diverse processing needs.
Onion Cold Storage
Ice Bank Refrigeration System
Air Cooling Units
Ice Bank Tank
Cold Storage Business Guide
Ammonia Refrigeration System
CA Cold Storage
Controlled Atmosphere Cold Storage
Apple Cold Storage
CA Cold Storage Chambers
IQF Technology
Ice Bank Chiller System
Individual Quick Frozen Technology
Blast Freezers
Blast Chillers
Curd Blast Rooms
Curd Incubation Room
Curd Incubation Chamber
Dairy Processing Plant
Cold Storage Explained
Ammonia Evaporators
Air Cooling Evaporators
Evaporators
Evaporative Condenser
Cooling Coils
Ammonia Cooling Coils
Ammonia Evaporative Condenser
Ammonia Air Cooling Units